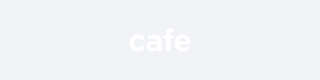
Ⅰ 블랭킹[Blanking]·피어싱[Piercing] 가공
블랭킹[전단]가공은 판재 면에 압축력을 가하여 최대파괴강도[UTS]에 이르게 함으로써 크랙[crack]을 유발시켜 파단 현상을 생기게 하여 판재를 분리하는 가공이다. 그림 1-1에서 펀치[punch]가 하강하여 재료의 표면에 접촉하면, 먼저 표면의 오목볼록을 고르는 자리잡기 공정을 한다. 더욱 하강하면 재료는 압축을 받아 인선[칼날]부근에 집중적으로 압축응력이 생겨 부분적으로 변형이 생긴다. 이 상태를 표시한 것이 (a)이며 초기 압축단계라고 한다. 다시 펀치가 하강하면 펀치는 점점 판을 내려 누르고 다이[die]는 점점 판을 떠밀어 올려서 그것에 비례하여 압축응력이나 인장응력도 증가한다. 이 상태가 (b)의 상태이다. 이때의 펀치 하강력을 p라고 한다면 p는 재료의 끝이 튀어 오르게 하는 회전모멘트[c×p=cp(㎏·㎝)]로서 작용한다. 그러나 재료는 펀치측면에 방해가 되거나 펀치 아래면의 재료의 저항과 만나거나 또는 판 누르개가 작용하거나 하여 실제로 회전하지 않고, 그 결과 굽힘 작용을 받게 되고, 그것에 대응한 인장응력이 생긴다. 다시 말하면 재료를 회전시키려고 하는 모멘트에 저항하는 힘이 생기게 되고, 이 힘을 p'라고 한다면 (c)와 같이 인선의 측면에서 대략 수평으로 작용한다.
요컨대 p와p'의 힘은 펀치 및 다이의 인선에서 쐐기로 작용하고, 펀치가 압력을 받아 하강하면 p 와 p'는 점점 증대하여 드디어 쐐기으로서 작용하는 힘이 재료의 파괴강도를 초과하므로 어떤 각도로서 균열이 재료에 생긴다. 그림(d)가 균열이 발생한 순간의 상태이다. 또 펀치가 하강하면 크랙은 점점 크게 발달한다. 드디어 펀치 및 다이의 양쪽에서 발달한 크랙은 어떤 곳에서 만나 절단은 모두 끝나게 된다. 전단과정에서 펀치의 행정과 펀치가 받는 하중의 관계를 나타내면 그림 1-2와 같이 되고, 이것을 펀치행정하중선도라고 한다. a까지의 부분이 그림 1-1(a)에 표시한 초기압축단계이다. 이점에서부터 그림에 표시한 바와 같이 하중은 갑자기 상승하여 b점에 도달한다. 여기가 그림 1-1(b)에 표시한 재료가 소성변형 하기 시작하는 단계이다. 판의 표면이 절단되기 시작하면 펀치가 받는 하중은 지금까지 보다 둔화되어 c점에 도달한다. 이 c점이 그림 1-1(d)에 표시한 크랙 발생의 단계이다. 일단 크랙이 발생하면 갑자기 저항력이 약해지고 펀치의 진행에 따라서 크랙도 급속하게 확대되어 가공이 끝난다. 이 크랙 발생의 시기 및 펀치측과 다이측의 어느 쪽 끝에서 먼저 발생하는가는 가공조건에 따라서 달라지지만, 보통의 전단가공에서는 먼저 다이측에 먼저 발생하고 이어서 펀치측에 발생하는 경우가 많다.
전단가공에서 클리어런스는 펀치와 다이 사이의 한쪽 편에서의 틈새이며, 그림 1-3에서 C 에 해당한다. 다이 및 펀치측에서 발생한 크랙이 제대로 합치되지 않으면 깨끗한 전단면이 얻어지지 않을 뿐만 아니라 가공력이 과대해지는 경우도 있다. 이러한 크랙의 진행 방향에 가장 중요한 영향을 미치는 인자는 클리어런스이다. 클리어런스가 적당하지 않으면
펀치와 다이가 잘 만나지 않고, 그 결과 과대한 압력이 생기거나 절단면이 판면에 대하여 큰 각도가 있거나 버나 처짐이 심하게 된다. 그림1-4는 블랭킹된 제품의 바깥 절단면을 확대한 도면이다.
a-처짐(rollover, shear-drop, penetrating), b-전단면(burnish), c-파단면(fracture), d-버(burr)로 구분한다. 그림 1-4에 표시한 형상은 클리어런스를 고려한 정상전단의 경우이지만, 클리어런스가 크고 작음에 따라서 이 형상은 그림 1-5에서 보여주는 바와 같이 변화한다. (a)는 클리어런스가 아주 작은 경우, 상하의 크랙은 빗나가서 그 사이에 가늘고 긴 부분이 생기게 된다. 인선이 더 먹어들면 사선부분은 다시 인선으로 깎아지게 되고, 외관은 그림에 표시한 바와 같이 버니시면이 2부분에 나타난다. 이 2번째의 전단형상을 특히 2차 전단이라 한다. 또한, 클리어런스가 과소한 경우는 처짐이나 캠버(camber)는 그다지 심하지 않고 버는 적은 특징이 있다. (b)는 클리어런스가 작은 경우이다. 크랙의 빗나감은 위의 것보다 감소하지만 완전한 합치는 이루어지지 않는 경우이다. 이 경우도 2차 전단을 부분적으로 하여 외관이 도면과 같이 버니시면이 드문드문 나타난다. (c)는 클리어런스가 적정한 경우로, 발생한 크랙의 만남이 잘 되어 어느 정도의 처짐, 캠버, 버 등이 있어도 전단면이나 파단면은 정상적인 상태를 나타내고 가장 좋은 상태이다. (d)는 클리어런스가 과대한 경우이다. 크랙의 끝이 합치하지 않으므로 판의 조직은 무리하게 찢어져서 조잡하게 되고 파단면이나 버가 많아진다. 클리어런스를 펀치 또는 다이에 주는 기본적인 원칙은 블랭킹한 제품은 다이의 치수와 같아야 하고, 피어싱한 구멍은 펀치의 치수와 같아야 한다. 즉, 제품의 외형이 정확한 치수를 요하는 블랭킹작업에서는 다이구멍을 치수대로 하여 펀치쪽에 클리어런스를 주고, 정확한 구멍치수를 필요로 하는 구멍뚫기 작업에서는 펀치를 지정치수대로 만들고, 다이구멍을 클리어런스만큼 크게 만든다. 적당한 클리어런스의 량은 재료의 종류, 경질, 연질 및 두께등에 따라 다르며 표 1-1과 같다. 일반적으로 경질재료, 두꺼운 재료 및 구멍뚫기의 경우는 클리어런스를 크게 하고, 연질재료, 얇은 재료, 정밀 블랭킹의 경우는 클리어런스를 작게 한다.
처짐 [roll-over] |
처짐은 전단과정에서 재료가 굽힙 변형을 받아 그 결과 인장을 받아서 생기는 재료의 얇아짐이다. 따라서 늘림이 큰 연질재, 클리어런스가 큰 경우, 인선이 무딘 경우에 처짐이 크게 나타난다. |
버 [burr] |
버의 크기도 처짐의 경우와 대체로 같으며, 클리어런스가 어떤 값 이상으로 커지고, 절인의 마모가 증가하고, 재료가 연질일수록 버도 증가한다. |
캠버 [camber] |
캠버는 전단과정 중에서 생기는 굽힘 모멘트가 펀치 아래의 재료를 만곡시키도록 영향을 주기 때문에 나타나는 것이므로 클리어런스가 큰 경우, 절인이 마모한 경우, 강성이 작은 연질재에 많이 나타난다. |
표 1-1 클리어런스의 참고치
|
사 용 목 적 재 질 |
정밀블랭킹 |
일반적 블랭킹 |
구멍을 펀칭 하는 것이 목적 또는 두꺼운 재료 |
금 속 | 고 탄 소 강
연 강 경 강 철 판 스테인리스강 동 (풀림) 동 (중경) 황 동(풀림) 황 동(중경) 인 청 동 알 루 미 늄 알 루 미 늄(경) 납 |
4 ∼12
2 ∼ 6 2 ∼ 4 1 ∼ 3 1 ∼ 4 1 ∼ 4 1 ∼ 4 2 ∼ 5 1 ∼ 3 1 ∼12 3 ∼ 6 |
12 ∼18 6 ∼ 9 8 ∼12 6 ∼14 4 ∼13 2 ∼ 9 3 ∼13 3 ∼10 3 ∼11 4 ∼11 3 ∼ 9 6 ∼18 5 ∼12 |
18∼26
18∼21 13∼24 8∼24 11∼24 9∼22 10∼24 7∼23 8∼21 14∼24 9∼23 |
비금속 |
에 보 나 이 트 셀 롤 로 이 드 패 놀 파 이 버 마 이 카 (운모) |
2 ∼ 3 | ||
직 포 종 이 |
가능한 작게 |
전단가공에 필요한 전단력을 알지 못하면 프레스기계에 과부하를 주거나 반대로 과대한 프레스를 사용하는 등 비경제적이다. 대략적인 최대 전단력 P(㎏)는 다음의 식에 의해서 계산한다.
P= σ×l×t σ : 전단저항(㎏/㎟), l : 전단되는 길이(㎜), t : 판두께(㎜) l×t : 전단되는 부분의 단면적(㎟) |
여기서 전단저항은 일반금속에 대해서는 인장강도의 약 75∼80%값으로 나타낸다. 표 1-1은 대표적인 재료의 클리어런스와 전단저항을 나타낸다. 이 전단가공력은 펀치 또는 다이면이 가압방향에 대하여 직각이면서 평평한 면인 경우에 한정된다. 시어각을 붙인 공구의 최대 전단력은 시어각의 크기에 따라서 달라지는데, 시어각을 붙이지 않은 것에 비해 20∼ 60%정도 감소한다.
시어각은 펀치 또는 다이에 붙인 경사각을 말하며, 전단력을 감소시키는 역할을 한다. 전단 가공력은 펀치의 하면이나 다이의 상면도 평평한 경우이지만, 이런 경우는 펀치의 압력을 분산시켜 큰 전단압력을 필요로 한다. 그러나 그림 1-6에서 보여주는 바와 같이 펀치와 다이에 경사를 붙이면 국부적으로 전단압력을 집중시켜 절단하므로 전단가공력과 충격은 감소한다. 시어각의 크기는 s 로 표시하며, (a)와 같이 다이에 시어각을 주었을때는 블랭킹한 것은 평평하고, (b)와 같이 펀치에 시어각을 주었을 때는 피어싱한 것은 펀치의 하면과 같은 형상으로 되고 남아 있는 블랭크는 평평하게 된다. 시어각에 의한 전단력의 감소는 클리어런스의 대소 또는 소재의 경질, 연질 그 외의 조건에 따라서 차이가 나타난다. 특히, 클리어런스를 크게 채용하는 경우는 시어각으로서 영향이 크게 나타나고 작게 채용하는 경우는 영향이 적다. 또한, 시어각의 양은 적어도 판두께와 같은 정도로 채용하지 않으면 효과가 적다. 시어각을 채용한 경우의 전단력 P(㎏)는 다음 식으로 구한다.
P= σ×l×t×c c : s의 대소에 의하여 결정하는 로마노프스키 계수 (s = t ⇒ c = 0.4∼0.6, s = 2t ⇒ c=0.2∼0.4) |
블랭킹 가공이 완료된 블랭크는 다이 안에서 내벽에 강하게 고착하는 성질이 있다. 이것은 캠버가 되돌아오거나 압축되어 있는 소재가 되돌아오기 때문에 생기는 현상이다.
그러므로, 다이의 단면이 입구나 출구가 같은 치수로 되어 있으면 블랭크가 다이구멍 안에 고착해 있다. 이렇게 블랭크가 다이 구멍에 남아 있으면 펀치의 소요압력은 다음 블랭크 가공에서는 차례로 증가하는 동시에 다이의 마모는 매우 빨라진다.
따라서 릴리프 각을 다이에 붙여서 1회의 블랭킹을 할 때마다 블랭크가 떨어지도록 하여야 한다. 이렇게 하면 펀치의 하중도 감소하고 펀치나 다이의 마모도 적어진다. 이 릴리프각을 붙이는 방법은 그림 1-7과 같이 (a), (b)의 2종류가 있다. (a)는 평행부를 남기는 방법이고, (b)는 인선에서 곧바로 빠지는 각을 붙이는 방법이다. (a)의 경우는 주로 박판에 사용하고 3∼5㎜의 평행부를 붙인 뒤 하부는 판두께에 따라서 표 1-2와 같은 릴리프각(N)을 붙인다. (b)는 다이 입구에서 곧바로 붙이는 방법이며, 1/2∼1˚정도가 일반적이지만 실제로 3˚가 한도이다.
|
표 1-2 판두께와 릴리프각
|
블랭크 배열은 재료의 이용률을 최대로 한 블랭크 배열, 버가 생기는 방향과 금형의 관계 및 이송피치와 잔폭의 결정을 의미한다.
(1) 배열과 재료의 이용률
재료에서 블랭크를 뽑을 때는 남아 있는 스크랩을 가급적 작게 하여야 한다. 이것은 소재의 이용률을 최대한 높게 하는 것이다. 그림 1-8은 L자 뽑기에서 4종류의 배열방법을 표시한 것이며, 각각의 1개당의 필요소재면적을 계산하면 다음과 같이 된다.
(a)=21.5×8.5 = 182.75 ㎟ (b)=19.5×6 = 117 ㎟ (64.0%) (c)=(26.5×8.5)÷2 = 112.63 ㎟ (61.6%) (d)=19.5×5 = 97.5 ㎟ (54.4%) |
(a) 면적을 100%로 볼 때, (b)-64.0%, (c)-61.6%, (d)-53.4%로 되어서 (d)는 (a)에 비교하여 이용율이 약 절반으로 상승한다.
(2) 블랭크 배열과 버의 방향
펀치가 닿는 면과 다이의 닿는 면에서도 버의 생기는 방법이 다르다. 그림 1-9와 같이 펀치측에 버가 나타나고 다이측이 아래로 처지기 때문에 둥글기가 생기는 것이다. 따라서, 대칭형이 아닌 부품의 금형에서는 하면 방향에서 본 펀치형상을 제품 표면형상으로 만들고 상면방향에서 본 다이구멍 형상과 제품의 뒷면 형상을 같게 만들어야 한다.
(3) 블랭크 배열과 롤 방향
재료의 압연방향도 블랭크 배열시에는 반드시 고려해야 한다. 특히, 블랭킹 후에 굽히는 부품의 블랭크는 주의하여야 한다. 압연 방향과 직각의 방향사이에는 인장강도나 연신율등에 많은 차가 있고, 가능한 롤 방향과 굽힘선과는 직각이 되도록 블랭크배열 하여야 한다.
(4) 잔폭
잔폭은 앞잔폭, 뒤잔폭 및 이송잔폭으로 구분되며, 그림 1-10과 같이 이송잔폭은 따낸 구멍의 끝과 다음에 따낼 구멍 끝과의 사이에 있는 나머지 폭이고, 테두리잔폭(앞잔폭, 뒤잔폭 또는 좌측잔폭, 우측잔폭)은 외형선과 직각인 방향으로 따낸 구멍의 사이에 있는 폭이다. 표 1-3은 표준적인 잔폭의 값을 나타내고 있으며, 표에서 알 수 있는 바와 같이 테두리 잔폭(B)은 이송잔폭(A)보다도 약 20∼50% 정도 많이 고려하는 것이 일반적이다. 또한, 테두리 잔폭은 판재의 두께와 같은 양 또는 1.5배보다 작은 경우는 재료가 인선에 의하여 미끄러지는 경향이 생긴다. 따라서 연질재는 경질재에 비하여 잔폭이 많이 필요하다.
컷오프 다이(절단 다이)는 절단 금형을 이용하여 소재를 직선 또는 곡선에 맞추어 한쪽방향으로 전단하는 가공이다. 그러나 컷오프다이는 소재를 한쪽방향으로 절단하므로 펀치에 가로의 압력이 걸린다는 결점이 있다. 그러므로, 컷오프다이의 경우에는 배면가이드 또는 펀치다리가이드가 있는 구조이어야 한다. 그림 1-12(a)는 판누르개가 있는 컷오프다이의 구조이다. 컷오프가공형식은 원래 스크랩이 없는 블랭크 배열법인데, 재료절약 측면에서 우수한 점은 있지만, 펀치의 수평압력이 걸려서 클리어런스가 크게 되고 그 결과 재료의 굽힘이 크게 된다는 결점이 있다. 또한, 버나 처짐도 많아지기 쉬우므로 배면가이드는 충분히 견고해야 한다. 컷오프가공에서 특히 주의하여야 하는 것은 (b)와 같이 버의 방향이 서로 반대방향으로 나타내는 것이다.
2-2 분할 전단금형(parting die) 또는 분단금형
분단금형은 절단하여 2개 이상의 단체부분으로 만드는 가공이다. 블랭크의 양측이 평행이며, 양끝이 이형의 경우에 응용할 수 있는 방법으로 그림 1-13은 전형적인 보기이다. 먼저 블랭크의 폭과 같은 치수로 전단한 짧은 판을 만들고, 다음 단면형의 펀치로 가로방향의 끝을 블랭킹함으로써 블랭크를 얻는 것이다. 그러나, 그림 1-14와 같이 긴 편의 치수로 짧은 판을 절단한 후 분단하는 방법도 있다.
분류 |
재단 폭을 좁게 하는 법(그림 1-13) |
재단 폭을 넓게 하는 법(그림 1-14) |
특징 |
• 큰 판에서 재단하는 횟수가 증가. • 재단할 때 비틀어져서 굽혀지기 쉬움. • 이송길이 증가하므로 생산속도 저하. |
• 분단용의 금형이 크게 되어 고가. • 제품정밀도가 좋고 생산성이 높음. • 수량이 적은 경우 금형의 비용 높음. |
블랭킹 금형은 소재에서 필요한 제품을 블랭킹하는 가공이며 구멍뚫기 가공과는 반대이다. 구멍뚫기 금형에서는 남아 있는 구멍 그 자체가 필요하지만 블랭킹금형에서는 뽑아 떨어트린 판재가 제품이다. 블랭킹 가공에서는 다이구멍을 제품치수대로 제작하고 펀치를 클리어런스 만큼 작게 만든다. 시어각은 다이편에 붙이고, 펀치의 하면은 블랭킹방향과 직각이어야 한다.
피어싱 금형은 소재에 구멍을 뚫은 가공이다. 피어싱 금형은 소재에 남아 있는 구멍이 목적이므로 펀치의 외주를 구멍과 같은 형상으로 만들고, 다이편에 클리어런스를 주어야 한다. 또한, 시어각을 필요로 하는 경우 펀치에 붙여야 한다. 그림 1-17은 평탄한 블랭크에 구멍뚫기를 하는 금형구조를 보여준다.
그림 1-18은 돌파형버링 금형 및 제품을 보여주고 있으며, 펀치끝을 피리밋 형상으로 연삭한 예리한 상태를 나타낸 것으로 버링이라고 한다. 그림 1-19는 버링제품으로 구멍뚫기와 버링의 2가지 동시가공으로 생기는 형상으로서, 구멍을 가공한 후 확대·성형하고 있는 것이다. 이 가공법을 피어싱·버링다이라 하고 작은 구멍의 버링에 많이 사용한다.
노칭금형은 재료 또는 제품의 일부를 절단할 때에 사용하는 것이며 컷오프다이의 변형이다. 노칭은 전단가공이므로 그림 1-20과 같이 화살표방향으로 펀치에 대하여 압력이 걸리므로 배면가이드가 반드시 필요하게 된다. 노칭다이는 가장 많이 프로그레시브다이(progressive die)의 전공정으로 사용한다.
2-7 슬릿 금형과 슬릿포밍 금형(slit die and slit forming die)
슬릿 금형은 판면에 슬릿선을 붙이는 랜싱(lancing)가공을 나타내며, 랜싱만의 가공으로 끝나는 것은 매우 적다. 랜싱가공이 사용되는 것은 프로그레시브다이의 연속드로잉에서 드로잉을 쉽게 하기 위해 필요한 블랭크 외형의 해당하는 곳에 슬릿선을 붙이거나 슬릿포밍을 위한 전제로서 사용하는 것이다. 또한, 슬릿 가공하여 한쪽 끝을 세우는 가공을 슬릿포밍이라고 한다. 그림 1-21은 1개의 창문을 여는 슬릿포밍다이를 표시한 것이다.
2-8 트리밍 금형(vertical type Trimming die)
수직절단 트리밍 금형은 슬라이드의 수직하강 운동에 의하여 직접적으로 테두리를 수직전단하므로 금형의 구조가 비교적 간단하다. 그림 1-22(1) 과 (2)는 플랜지를 남기는 경우의 0트리밍용 금형이며 ⑴은 제품을 안내에 덮고 테두리를 전단하는 방법이고, ⑵는 제품을 안내구멍에 떨어뜨려 놓고 테두리를 전단하는 방법이다.
2-9 트리밍 금형(horizontal type Trimming die)
수평절단 트리밍 금형은 제품의 수직벽에 대하여 수평방향에서 전단력을 가하여 끝부를 잘라 내는 방법이며, 그림 1-23은 가장 대표적인 캠트리밍다이의 구조이다. 캠은 하형에 내장되어 있으며, 펀치끝의 코어를 제품에 끼워서 일정한 깊이까지 들어가면 아래로 누르는 블록이 다이의 상면을 내려 누른다. 그 때문에 다이의 주위에 설치한 캠이 펀치 절인에 대하여 상대적으로 전후좌우로 움직인다. 제품은 내부의 코어와 외부의 다이와 일체로 되어, 전후좌우로 움직이므로 펀치의 하면과 다이 상면으로서 수평으로 트리밍한다.
셰이빙 금형은 블랭크 절단면의 상태는 처짐, 전단면, 파단면, 버 등이 나타나고, 판면에 대하여 직각의 절단면이 아니고, 깨끗한 다듬질면으로 되어있지 않으므로 이러한 표면을 다듬질하는 것이 셰이빙 가공이다. 셰이빙 가공에는 외형 셰이빙과 내형 셰이빙이 있다. 일반적으로, 셰이빙이라는것은 외형다듬질의 경우이며 가공법으로는 그림 1-24와 같은 펀칭낙하형식의 2종류와 거꾸로 형식의 1종류 가공법이 있다. 셰이빙 가공법은 버가 있는 면을 향하여 판두께의 5∼8% 정도씩 깎아내는 것이지만 문제로 되는 것은 벗기기의 빠지기가 가능하게 되도록 금형구조를 생각해야 하며 이점에 있어서는 역(거꾸로) 형식의 편이 우수하다. 따라서 가능한 한 역 방식을 채용한 금형을 만들어야 하지만 이것에는 제품을 고정하는 구멍 등이 필요하다. 또한, 셰이빙 금형 가공법에 주의할 것은 다이구멍에 릴리프각을 설치하는 것이다. 구멍의 안쪽을 약간 작게 만들어 가공품을 무리하게 눌러 넣고 다이구멍의 주위에서 제품외주를 깨끗이 깎아야 한다.
브로치 금형은 절삭가공에서 사용하는 브로치와 같은 절인을 펀치에 붙여서 구멍이나 홈의 내부벽을 깨끗이 다듬질하거나 치수정밀도를 올리거나 하는 가공법이다. 그림 1-25는 기어의 축구멍에 브로치로 키 홈을 깎는 방법을 표시한 것이다.
3-1 단식 전단다이(single type punching die)
단식전단 다이는 펀치와 다이가 1개씩의 간단한 전단금형이고, 단능형, 단발형이라고도 하며 금형구조로서는 가장 근본적이고 비능률적이다. 그러나 일면으로는 제작하기 쉽고 수리도 간단하다는 특징이 있다. 프로그레시브 다이나 콤파운드다이와 같이 복잡한 금형을 제작하는 것보다도 단식전단의 금형으로 구성된 세트를 만드는 것이 납기가 빠르고 금형비도 낮은 것이 일반적이다.
3-2 다열 펀칭다이(multi type punching die)
다열 펀칭다이는 같은 형상의 2개∼여러개 펀치를 나란히 프레스의 1개 행정으로 설치하여 같은 제품이나 같은 구멍을 동시에 가공하는 금형구조이다. 그림 1-26은 기본적인 원형 블랭크의 3렬따기 금형이다.
3-3 프로그레시브 다이(progressive die)
프로그레시브 다이는 여러 공정이 걸리는 1개의 제품에서 생산성을 올리기 위하여 2공정 ∼여러 공정을 직렬로 나란히 1개의 형으로 조합한 가공법으로 일반적으로 1행정으로 1개의 완성품을 만드는 것이 보통이다. 그림 1-27(a)는 와셔따기의 프로그레시브 다이이다. 즉 1 공정은 피어싱하고 2 공정에서 블랭킹을 하는 2공정형이다. 1공정에서 뽑은 구멍의 버와 2공정에서 뽑은 제품 외주의 버는 역방향으로 된다. 1공정에서 뚫은 구멍이나 내형을 파일럿 등으로 안내하므로 약간의 틈이 존재한다. 컴파운드 다이 형식에 비교하면 정밀도가 떨어지는 결점이 있다. 각 공정을 일시적으로 스톱하여 가공하는 위치를 스테이지 또는 스테이션이라 한다. 2공정으로 제품이 끝나는 초보적인 프로그레시브 다이를 특히 2스탭다이(two-step die) 또는 탄뎀다이(tandem die)라 한다. 또한, 피어싱 후에 블랭킹을 하는 프로그레시브 다이를 프로그레시브 블랭킹??피어싱 다이라고도 한다. 프로그레시브 다이에서 주의할 점은 앞 공정에서 뚫은 구멍과 최후의 블랭킹의 상대적 관계가 정확하게 되도록 배치하여야 하는 것이며 그 역할을 담당하는 것이 파일럿 핀이다. 그러므로, 파일럿핀의 형상, 정밀도는 매우 중요하며 프로그레시브가공의 정밀도를 좌우한다.
콤파운드 다이는 피어싱과 외형을 소재의 이동 없이 가공하는 금형이다. 즉, 피어싱 금형과 블랭킹 금형을 조합한 것이며 그림 1-28은 상형에 펀치와 다이에 해당하는 것이 있고, 하형도 피어싱이 다이에 해당하고 외주가 펀치에 해당하는 형식이다. 그림 1-28(a)은 재료를 삽입하여 블랭킹으로 옮기려고 하는 경우를 표시하고 그림 1-28(b)은 제품의 블랭킹이 끝난 순간을 표시한다. 도면부호의 1은 구멍뚫기 펀치, 2는 구멍뚫기 다이를 겸한 블랭킹 펀치, 3은 블랭킹 다이이다. 블랭킹한 제품은 3의 안에 끼워져 버리므로 스프링의 힘으로 4를 밀어 떨어트려서 제품이 튀어 나오게 하고 스크랩판은 2의 주위에 밀착한다. 이것도 스프링 력으로 5를 떠밀어 올려서 벗겨지는 구조로 되어 있다. 콤파운드 다이의 장점은 정밀한 제품이 얻어지는 것으로, 프로그레시브형은 파일럿 지름이 구멍지름보다 약간 작아야 하므로 콤파운드 다이와 비교하면 정밀하지 못하다. 또한, 4와 5에서 재료를 정확하게 누른 뒤에 전단작업을 하므로 제품이나 스크랩도 평평한 것으로 된다.
펀치가이드는 상형을 하형의 내부로 안내하며 행정과 직각의 방향에는 양자의 관계위치가 어긋나지 않도록 하는 역할을 한다. 펀치가이드의 형식은 다음의 2가지로 분류된다.
직접 가이드 형식 |
① 힐 펀치 가이드식 ② 힐 블록 가이드식 ③ 스트리퍼 플레이트식 |
간접 가이드 형식 |
① 다이세트식(가이드 포스트식) |
펀치와 프레스의 연결방법도 일반적으로 다음과 같이 두 가지로 분류된다.
직접 강성적 방식 |
▶ |
펀치가이드가 없는 금형구조 |
▶ |
생크 가압력 전달방식 |
간접 강성적 방식 |
▶ |
펀치가이드가 있는 금형구조 |
▶ |
프레스의 가압력 전달식 |
펀치가이드가 없는 금형 구조에서는 일반적으로 강성연결로 하여 프레스기계의 정밀도로서 금형의 맞춤을 유한다. 그러나 다이세트와 펀치가이드를 병용하는 금형 구조에서는 금형의 맞춤은 정밀한 다이세트의 가이드에 의존하고 펀칭력은 프레스의 가압력에 의존한다.
프레스 슬라이드와 펀치 사이의 연결은 대부분은 둥근 생크를 사용한다. 생크의 형상과 치수의 비율을 공업규격은 그림 1-29 및 표 1-4와 같이 결정하고 있다. 일반적으로, 슬라이드의 생크 설치부(생크 누르개)는 그림 1-30과 같이 분할되어 있고, 이렇게 하면 생크 바깥면에 대한 마찰면이 커지므로 설치가 견고하게 된다. 이 구조에서 중앙의 누르기 볼트는 생크 고정의 역할도 하지만, 본래의 목적은 빠져 떨어지는 것의 방지이며, 고정은 생크 누르기개 내면에 의한 마찰력이다.
(1) 일체형 펀치·생크 및 단체형 펀치·생크 구조
일체형 펀치·생크 구조는 그림 1-31에서 보여주는 바와 같이 펀치에 직접 생크를 내는 방법이며 가장 안전한 구조이다. 그러므로, 펀치가 원형인 경우는 선반만으로 간단하게 일체의 것을 제작할 수 있기 때문에 이 방법을 많이 사용한다. 그러나, 생크의 지름에 비교하여 펀치지름이 매우 큰 경우에는 생크를 절삭하기 위하여 처음의 재료가 예상외로 크게 되고, 절삭에 많은 시간이 소요된다. 단체형 펀치·생크 구조는 그림 1-32에서 보여주는 바와 같이 펀치에 생크를 고정한 경우로서, 펀치홀더를 특별하게 만들지 않고 펀치에 생크를 나사로 직접 고정한 것이다.
(2) 펀치홀더에 생크의 고정
펀치홀더는 펀치를 설치하는 대판 부분을 말하며, 그림 1-33은 펀치가 여러 개 있고 펀치가 비교적 클 때 펀치플레이트를 사용하여 고정한 구조이며 가장 일반적이다. 펀치홀더의 면적이 큰 경우, 생크를 별도로 만들어서 결합하는 방법을 사용하고 있으며, 그림 1-34에 대표적인 4가지 예를 보여주고 있다. (a)-코킹결합. (b)-생크를 나사로 고정한 뒤 뒷면에서 구멍지름보다 약간 굵은 핀을 박아 넣는 방법. (c)-플랜지 붙은 생크를 나사 고정한 후 회전정지 핀으로 고정하는 방법. (d)-압입감합.
힐 펀치가이드 금형 방식은 그림 1-35에 나타낸 바와 같이 펀치에 특별히 힐(heel)이 나와 있고 전단이 개시되기 전에 힐이 다이 안에 돌입하여 펀치와 다이의 관계위치를 결정하고 전단 작업 중에 펀치가 압력을 받아도 펀치가 움직이지 못하도록 한 금형구조이다. 이 구조는 주로 노칭다이에 응용된다.
힐블록가이드 금형 구조는 그림 1-36에서 보여주는 바와 같이 한쪽편 절단의 경우에 펀치의 움직임을 방지하는 것을 목적으로 한다. 힐블록가이드 형식은 다이의 일부가 압력을 받는 가이드로 되어 있다.
스트리퍼 플레이트 가이드 금형은 다이와의 사이에 재료가 통과하는 틈만을 남기고 다이와 평행하게 장치한 판에 가이드구멍을 뚫은 것이며 구멍은 펀치가 들어갈 수 있도록 되어 있다. 그림 1-37이 펀치가이드를 붙인 금형, 즉 스트리퍼 플레이트 가이드금형이며, a가 펀치가이드용 스트리퍼 플레이트, b가 가이드레일, c가 다이이다. 가이드 플레이트는 충분히 두껍게 만들지 않으면 가이드로서의 효과가 적다. 두꺼운 판을 펀치의 복잡한 형상에 맞춰서 구멍의 내면을 상하평면에 대하여 정확하게 직각으로 다듬질해야 한다. 그리고, 가이드 구멍은 펀치에 대하여 클리어린스가 있어서는 안 된다. 또한, 스트리퍼 플레이트 가이드 형식은 정밀도가 높은 가공에서 다이세트와 병용하여 사용하는 것이 바람직하다.
다이세트 형식은 A형(JIS)을 제외하고는 펀치와 다이를 조합한 대로 프레스기계에서 사용할 때 곧바로 사용하도록 되어 있는 1조의 세트이다. 펀치와 다이는 각각 홀더에 고착하고 그 홀더는 1개∼여러 개의 가이드포스트로서 항상 같은 관계위치를 유지하면서 상하에 슬라이드하는 것이 특징이다. 단, 다이세트라는 것은 펀치와 다이를 제외한 홀더부분만의 것을 말하며 그림 1-38은 다이세트의 구성요소이며 장점은 다음과 같다.
① 프레스에 금형을 설치하는 데 시간이 많이 걸리지 않는다. ② 형 맞춤에 숙련이 필요하지 않다. ③ 클리어런스를 유지하기 쉽고 깨끗한 제품을 만들 수 있다. ④ 작업 중은 물론 작업외의 운반, 설치, 제거, 보관에 있어서 금형의 손상이 적다. ⑤ 정밀도가 매우 나쁜 프레스에도 사용 가능하다. ⑥ 금형의 수명이 길어진다. ⑦ 다이세트로서 보강하므로 금형이 얇아도 사용할 수 있다. |
다이세트의 형식은 그림 1-39에서 보여주는 바와 같이 A형 이외의 JIS규격에서 정한 4가지 형식이 있지만, 부시 부착의 경우는 BB형, CB형, DB형, FB형으로 되고, 볼을 넣는 경우는 BR형, CR형, DR형, FR형이라 한다. B형은 앞쪽과 좌우의 세 방향이 열려 있으므로 작업하기 쉬운 형상으로, 특히, 형상이 불균일한 스크랩을 사용하는 블랭킹작업을 할 때에 편리하다. 그러나 강성의 점에서는 다른 형식보다 나쁘다. C형은 강성의 점에서는 우수하지만 좌우이송이 불가능하다. D형은 강성의 점도 어느 정도 합리적이고 또한 이송도 전후좌우 다 가능하여 편리한 형상이다. F형의 4개 포스트는 강성의 점에서는 가장 우수한 구조이다. 그러나 4개의 포스트를 정확하게 맞춘다는 것은 매우 어려운 일이고 제작에 고도의 기술을 요한다는 결점이 있다.
기름 홈은 덩굴감기형도 좋지만 머리띠형 쪽이 기름을 흘려 버리지 않으므로 좋다. 부시는 홀더의 슬라이드 부분이 주물이라면 반드시 필요하지 않지만 따로 있는 편이 내부마모에 대한 수리가 쉽고 가이드포스트의 보호도 되므로 청동, 포금 등으로 만드는 것이 보통이다. 또한, 그림 1-40과 같이 부시의 상면내주는 모서리따기하여 기름 괴는 곳을 만들어야 한다. 부시의 길이는 포스트지름의 2배 정도가 좋다. 가이드포스트는 다이홀더에 단단하게 고정하는 것이 일반적이지만, 다이를 연마하기 위해서는 펀치홀더에 고정하는 것이 편리하다. 그러나 펀치홀더에 포스트를 고정하는 것은 드로잉한 제품의 밑바닥에 구멍이 똟려 있거나 테두리를 절단할 때는 가이드포스트가 하형의 부시에서 빠져나와 오히려 위험하므로 사용하지 않는 편이 좋다. 프레스에는 추력만 담당하게 하고 펀치와 다이의 형맞춤은 가이드포스트에 담당시키는 연결방법이 필요하다.
캠 금형에서는 펀치를 프레스 슬라이드의 운동방향과 직각으로 움직이게 하는 경우이며 펀치를 수평펀치(횡펀치)라고 한다. 용기류의 측면에 여러 개의 구멍을 동시에 뚫는 작업은 이 수평펀치형식을 사용하면 매우 효과적이다. 이와 같은 펀치의 운동은 기계적으로는 대부분 캠기구로 하고 있기 때문에 캠다이라고 하는 경우도 있다. 캠의 구조는 그림 1-41에서 보여주는 바와 같이 (a)-쐐기식, (b)-내확식, (c)-게다리식, (d)-경사다리식으로 구분한다.
(1) 쐐기식 캠 수평펀치금형
쐐기식 캠 수평펀치금형은 그림 1-42에 표시한 구조형식의 금형이며 기둥이 직선으로 되어 있고 그 끝이 경사로 깎은 캠의 작용을 하고 있다. 이 형식은 가장 간단하지만 펀치를 당겨 되돌리는데 스프링의 힘을 이용해야 하는 것과 그 스프링이 바깥쪽에서 돌출되어 금형 전체가 큰 면적을 차지하는 결점이 있다.
(2) 게다리식 캠 수평펀치금형
게다리식 캠 수평펀치금형은 그림 1-43에 표시한 구조형식의 금형이며 캠의 다리가 게의 형상과 비슷하므로 게다리식이라고 한다. 보통 다량생산의 경우는 작동 고장이 적으므로 이 형식이 바람직하다.
(3) 토글식 수평펀치금형
토글식 수평펀치금형은 그림 1-44에 표시한 구조 형식의 금형이다. 특징은 축핀부분을 정확하게 만든다면 행정의 최소점과 최대점이 정확하고 또한, 최대점 직전에 최대의 추력을 발휘할 수 있다는 이점이 있으므로 전단작업이나 코이닝작업 등에 적합한 구조이다.
특수전단 금형은 아래와 같은 경우에 일반적으로 사용하며 종류는 다음과 같다.
o 지름이 큰 둥근 펀칭의 경우 o 원형의 일부가 빠지고 있는 경우 o 정사각형 또는 직사각형의 경우 o 좌우대칭형 블랭킹구멍의 경우 o 블랭킹구멍의 폭이 좁은 경우 o 일부분이 가늘게 돌출하고 있는 경우 o 원주가 어떤 단위의 같은 형상으로 되어있는 경우 o 금형이 크고 복잡한 경우 |
분할 다이는 펀치 또는 다이를 한 재료에서 가공하지 않고, 2개 또는 여러 개로 분할한 금형으로, 아래와 같은 경우에는 분할형이 합리적이다.
첩부금형은 그림 1-45에서 보여주는 바와 같이 펀치 및 다이의 몸체는 연강판을 산소 절단한 채로 사용하고, 인선으로 되는 부분은 3∼5㎜두께의 게이지 강판으로 만들어서 연강판의 몸체에 점 용접으로 산소 용접한 구조이다.
경사펀치 금형은 그림 1-46에서 보여주는 바와 같이 펀치가 수직이나 수평도 아니고 경사각으로 운동하는 경우이다. 이 금형의 가장 큰 특징은 펀치가 프레스 슬라이드에 설치되어 있지 않고 자유상태로 있으며 그 머리를 캠블록으로 두둘겨서 구멍뚫기하는 것이다.
유닛 금형은 그림 1-47에서 보여 주는 바와 같이 펀치, 다이, 스트리퍼 등의 구조부분이1세트로 되도록 특별한 홀더 안에 조립한 금형이다.
덧살붙이기 금형은 그림 1-48에서 보여주는 바와 같이 몸체를 연강판으로 만들고 인선부분만 산소용접으로 합금강을 덧살 붙인 구조이다. 최근 모재를 보통 주철(FC)로 제작하고 그것에 덧살을 붙여서 블랭킹 다이로 하는 방법이 자동차부품의 금형에서는 이미 실용화의 단계에 있다. 이 금형의 가장 중요한 문제점은 주철에 접하는 아래 덧살층의 밀착이며, 보통은 니켈순도 99.7% 정도의 용접봉을 사용한다.
고무블랭킹 다이는 그림 1-49에서 보여주는 바와 같이 금형을 필요로 하지 않으며 게이린법(Guerin process)이라고도 한다. 먼저 프레스베드 위에 블랭킹하려고 하는 형상과 같은 형상의 두께 6㎜정도의 담금질한 강판을 올려놓고, 다음에 전단할 연질의 박판을 그 위에 포개고 또 그 위에 고무판을 얹어 놓고 위에서 액압 프레스등으로 압력을 걸면 형판인 강판은 예리하게 모서리가 나 있기 때문에 재료는 예리한 각에서 굽혀지고, 형판 밖으로 삐져 나온 금속판은 베드면과 고무판의 사이에 끼워져서 재료를 주위의 방향으로 약간 인장하고 형판의 모서리에 응력을 집중시켜서 재료를 파단한다.
(1) 스톡가이드
스톱 가이드는 가공하는 재료나 블랭크의 위치 결정하는 역할을 담당한다. 특히, 2차 가공에서의 위치결정에서는 로케이션핀이나 로케이션 플레이트 등의 호칭법도 사용한다. 그림 1-50은 백게이지 형식이며 재료판이 단척판 또는 코일판일때 사용하는 가이드이다. 즉 재료의 안내를 하는 백게이지를 주체로 하여 지지판(stock rest)과 프론트게이지(스페이서)로서 구성되어 있다. 백게이지와 프론트게이지의 간격은 재료판을 부드럽게 통과시키기 위하여 재료판의 폭치수보다 약간 크게 만들어야 한다.
(2) 스톱핀
스톱핀은 다이에 가는 핀을 끼워 넣어서 소재의 이송을 일정하게 분배하는 형식이고 보통 핸드이송작업용으로 사용하는 형식이다. 그림 1-51은 철사의 머리부를 직각으로 굽혀서 다이블록에 튼튼하게 고정한 스톱핀이다. 그러나 다이구멍의 가까이에 별도로 구멍이 있는 것은 담금질균열이나 가공시에 충격크랙의 원인이 되므로 가능한 한 피해야 한다.
(3) 자동스토퍼
자동스토퍼는 여러 가지 형식이 있지만, 그림 1-52는 가장 실용적으로 사용하고 있는 형식이다. 소형품의 연속 블랭킹가공에서의 스토퍼로서 핸드이송이나 자동이송도 함께 많이 사용할 수 있는 구조이다.
(4) 사이드컷 펀치
사이드컷 펀치는 재료판을 이송할 때 한쪽측 또는 양측을 이송 피치와 같은 길이로 노칭하고 그 노칭으로 생긴 단을 형의 벽에 부딪쳐서 이송피치를 결정하는 방법이다. 이 방법은 이송량이 적고 정밀도를 필요로 할 때에 적합하다. 그림 1-53에서 d부의 해칭선은 제품의 펀치구멍, S부의 해칭선은 사이드컷 펀치의 펀치구멍을 각각 표시하고 있다. 이 그림에서 사이드 컷은 한쪽편용이며 노칭으로 새로 생긴 단을 스토퍼에 밀어붙임으로써 제품 펀치구멍의 피치를 결정한다.
(5) 파일럿
순차이송형에서 재료판을 이송하는 것은 자동이송장치로서 하고 그리고, 일정한 위치에 정지시키는 것은 스토퍼로서 하지만 정지할 때 다소의 처짐이 발생한다. 이 처짐을 수정하는 것이 파일럿이며 순차이송형에서는 매우 중요한 요소이다. 파일럿에서는 그림 1-54(a)와 같이 펀치 그 자체에 붙이는 직접식 파일럿과 그림 1-54(b)와 같이 전용의 파일럿으로 위치수정을 하는 간접식 파일럿 2가지가 있다. 정밀도와 강도의 점에서 보면 직접 파일럿을 사용하는 것이 우수하다.
(6) 고정 스트리퍼
고정 스트리퍼는 그림 1-55(a)와 (b)에서 보여주는 바와 같이 다이측에 설치하는 대표적인 2종류가 있고, (a)는 소량의 간이형에 주로 사용하는 것이며, (b)는 폭이 결정되어 있는 단척재 또는 코일재를 블랭킹 하는데 사용한다.
(7) 가동 스트리퍼
가동 스트리퍼는 그림 1-56에서 보여주는 바와 같이 스프링 패드 또는 프레셔 플레이트라고 하는 판으로서 가공재를 눌러 붙여놓고 블랭킹한 뒤의 펀치상승에서 가공품을 낙하시키는 형식이다. 스프링으로 가동하도록 되어 있으므로 스프링 스트리퍼라고도 말한다. 또한, 이 형식을 사용하는 큰 이유는 블랭크의 삽입 및 취출이 쉽다는 것이다.