표면처리
1. 기초이론 금속표면처리의 목적은 부식을 방지하는 방식성, 색채 및 광택을 향상시키는 장식성, 경도, 내마모성, 내열성 등을 향상시키는 기능부여 등을 근본적인 목적으로 하고 있다. 금속표면처리의 종류에는 도금, 양극산화, 화성처리, 도장, 라이닝, 코팅, 표면경화 등이 있다.
1.1 도금(Plating) 금속의 표면이나 비금속 표면에 다른 금속을 사용하여 피막을 만드는 처리이며, 처리방법으로서는 전기도금, 화학도금, 용융도금, 진공도금, 침투도금, 이온도금 등이 있다.
1> 전기 도금 전기에너지를 이용하여 금속 또는 비금속 소지에 다른 금속의 피막을 만들어 주는 방법이며, 용도로서는 장식품, 공업용품등 용도가 가장 넓다.
2> 화학 도금 화학변화를 이용하여 금속 또는 비금속 표면에 다른 금속의 피막을 만들어 주는 방법이며, 용도로서는 플라스틱 제품, 금속제품의 일부위에 도금하는데 사용된다
3> 용융 도금(Dipping Plating) 금속을 도금하고자 하는 금속의 용융체에 담가서 용융금속의 피막을 만들어주는 방법이며, 용도로서는 아연 및 주석 도금강판, 아연도 파이프 등에 이용된다. ― 현재 Zn이 이온상으로 Fe위에 도금 ― Zn 및 Sn 도금 강판, 아연 도금 파이프 등에 이용됨
4> 진공 증착도금(Evaporation Deposition) 금속 또는 비금속 표면에 다른 금속을 진공내에서 증발시켜 금속 피막을 만드는 방법으로서, 용도로서는 각종 플라스틱 장식품, 장신구, 렌즈등에 사용된다. (증발 가스가 직선 운동을 하기 때문에 밀착성이 낮다) (Noble metal Coating)
5> 침투 도금(확산도금) 금속에 다른 금속을 확산침투 시켜서 합금의 피막을 만들어 주는 방법(Carburizing, Nitriding)이며, 용도로서는 내식 및 내열등의 목적에 사용된다.
6> 이온 도금(Ion Plating) Glow 방전으로 금속이나 가스를 (+)로 이온화시키고, (-)로 가속하여 음극소지에 피막을 만드는 방법으로서, 용도로서는 각종 금속, TiN, TiC등으로 내열, 내마모성 피막생성, 금색 코팅에 사용된다.
7> 음극 스퍼터링(Cathode Sputtering) 진공 내 플라즈마 중에서 Ar+이온(+)의 입자로 음극물질을 때림으로서, 음극물질이 튕겨 나온 것이 진공내의 피도금물체에 피막을 만들게 되는 원리이며, 용도로서는 전자, 자동차부품 등 금속 및 비금속위의 금속피막을 만드는데 사용된다. (밀착성이 매우 강하다.) (레코오드판, 전자, 자동차 부품, 박막 제조 등에 이용됨.)
8> 금속 용사(Thermal Spraying) 금속 표면에 다른 용융금속을 분무기로 뿌려서 피막을 만들어 주는 방법이며, 용도로서는 유류 탱크 및 탱크의 내부, 마모된 부분의 보수등에 사용된다.
9> 하지 도금 금속표면에 최종도금을 하기 전, 도금물질과 소지의 밀착성이 좋지 않을 경우에 그 사이에 최종도금을 하기 위한 목적으로 도금해주는 것을 말한다. (Fe에 Cr 도금이 잘 되지 않으므로 Cu를 먼저 도금한 다음 Cr 도금을 함.) (공해문제가 단점)
1.2 화성처리(chemical coating) 금속 표면에 일종의 화학피막을 만들어 주는 화학적인 처리를 말하며, 처리방법으로서는 인산염 피막처리, 크로메이트 처리, 착색등이 있다.
1> 정의 금속 표면에 화학 변화를 일으켜서 인산염(인산망간, 인산 아연, 인산철 피막 등과 복합 피막)피막 또는 산화 피막 등을 제조함. 방식 및 도장 하지용 피막, 금속 착색 등에 이용됨.
2> 내용 ― sintering (고체의 경우 반응이 느림) ― 고체 : diffusion 이동 ― 액상 : ion 이동 ― 기상 : 분자상 이동
3> 인산염 피막 ― Mn염 사용, 공구에 주로 이용, 방청, 도장 하지 처리, 마모 윤활
4> 크로메이트 처리 아연 도금의 단점을 보완하기 위하여 표면에 Cr의 착화합물을 형성하여 내식, 색상, 광택의 성질을 얻기 위한 처리 방법
1.3 양극 산화 피막(Anodizing) 금속물체를 양극으로 하여, 전기화학적으로 산화피막을 만드는 피막이며, 주로 Al의 산화피막에 널리 사용되고 있다.
1> 정의 ― Anode에서 전기 화학적 산화 피막
2> 내용 - Al 피막 : Al2O3(구조용, 광학용 재료) - Al을 Anodizing처리하면 육각형 모양으로 되어 산소가 더 이상 통과하지 못하며 filter의 기능도 가능
Thermal barrier coating ·열 혹은 전기를 차단 즉 집중되지 않게 퍼트리는 역할. (Al2O3를 이용함. 기능 코팅으로써, 코팅재의 방향성이 요구됨.) ·컴퓨터의 경우 main칩의 보호를 위하여 thermal barrier coating을 한다. (Al2O3, Diamond) ·인공위성의 경우에 사용된다.
1.4 Painting(도장) 부식을 방지하는 동시에 미관을 주기위한 목적으로 금속의 표면에 도료를 칠하는 방법을 말한다. ― 금속표면에 도료를 도포하여 방식과 미관을 좋게 하는 방법 ― 각종 철물의 기계 구조 및 건축물 등에 이용됨
1.5 lining 금속으로 만든 탱크등의 내면에 납판, 고무, 합성수지등을 피복시키는 것을 말한다. ― 금속 표면에 고무나 합성 수지 등의 피복을 해 주는 방법 ― 화학 장치류, 도금 탱크 등에 이용됨
1.6 표면 경화 (Case hardening) 탄소나, 질소등을 침투시켜서 표면을 경화 또는 기타의 방법으로 물리적 성질을 향상시키는 방법을 말한다, 그러나, 이 처리방법은 주로 금속 열처리 분야에서 취급하고 있다. ― 금속 표면에 C, N을 침투시켜서 경도가 큰 피막을 만들어 주는 방법 ― 기어 등 내 마모성과 경도를 표면에 요하는 부속품 등에 이용됨
1.7 Coating 금속표면에 합성수지 또는 법랑(enamel), 세라믹 같은 투명 수지 피막 또는 유리질 피막을 만드는 방법이다. ― 금속 표면에 투명 수지 피막 또는 유리질 피막을 만드는 방법 ― 금속의 방식, 도금의 색상 유지, 법랑 등에 이용됨
1.8 전해에 미치는 요소
도금시 저전류밀도에서는 결정의 성장속도가 커서 거친도금이 되고, 적당한 전류밀도에서는 미세한 결정의 미려한 도금이 된다. 고전류밀도에서는 음극부근의 이온농도 저하로 결정성장이 비교적 농도가 큰 부분에서만 일어나, 수지상 결정이 생기며, 과고전류밀도에서는 구멍이 많은 스폰지상 도금, 심하면, 분말상도금이 된다.
― 저 전류 밀도(거친 도금) ― 고 전류 밀도(수지상 결정)
1> 액농도 교반속도,
고농도 및 교반시는 고전류밀도에 의한 미려한 도금가능하게 된다.
― 물질 이동 속도 증가시킴
2> 전해온도
온도를 높게 하면, 전도율이 커져, 고전류밀도 사용가능하고, 수소흡장, 내부응력감소가 되나, 전착물의 결정이 크게되고, 경도가 낮아지며, 균일 전착성이 떨어진다.
― 고 전류 밀도 사용 가능, 수소 흡장, 내부 응력 감소,그러나 경도 저하, 균일전착성 저하 유발함.
3> 첨가제
첨가제를 첨가해서 도금층의 평활화, 미세화, 광택부여, 전착응력감소, 피트 방지등과 균일 전착성 개량 등을 행한다. 첨가제는 보통 미량첨가하게 되어 있다.
― 도금층 평활화, 미세화, 광택 부여, 전착 응력 감소, 피트 방지
전처리
일반적인 전처리 공정 연마 → 예비세정 → 알카리 탈지 → 전해탈지 → 수세 → 산세 → 수세 → 활성화(또는 중화)처리 → 수세 → 스트라이크 → 수세 → 도금.
2.1 연마
연마의 종류에는 버프연마, 바렐 연마, 샌드블라스트, 쇼트블라스트, 액체호우닝, 래핑, 벨트 연마, 전해 연마, 화학연마등이 있다. 연마는 전기도금의 전처리로서 중요한 단계이며, 조연마와 피니싱연마(중연마와 광연마)로 분류할 수가 있다.
1) 목적 : 도금 밀착성 및 평활성 향상.
2) 조 연마(grinding) 천, 펠트, 가죽 등으로 만든 회전체에 연마재(용융알루미나, 에머리 등)을 아교, 아브레이시브 시멘트(abrasive cement)등의 접착제를 고착해서 만든 연마공구를 고속도로 회전시켜서 도금할 표면을 접촉연삭하는 가공법을 말한다. 따라서, 조연마를 하게 되면, 도금할 물건의 표면의 거시적인 요철을 평활하게 깍아 내리며, 버프(buff)표면에 접촉시킨 에머리의 입도의 크기와 접촉방법에 따라서 조연마면의 줄의 홈(눈, 메)의 깊이가 달라진다. 이 깊이가 클수록 그후의 피니싱연마까지 완전광택을 얻는데 고생을 하게 된다.
3) 완성 연마(polishing) 이 연마에서는 조연마로서 거친 면을 편편하게 깍을 때 면이 에머리에 의해서 생긴 홈을 중연마(cutting down)에서 몇 단계의 고은 에머리 버프연마에 의해서 점차 가는 홈(finer scratch)으로 만들고, 최후에 유지 연마제로 광택있고 홈이 없는 완성면을 얻도록 한다. 그 최후의 광택있는 연마를 광연마라 한다. 조연마 때와는 달리 표면으로 갈수록 결정입자가 미세하게 되었으며, 이것은 버프의 압력에 의해서 볼록 부분이 오목부분으로 밀려간 것이고, 이때 열이 발생하여 용융상태로 유동되었다고 생각할 수가 있다.
cf) 비 결정층(Beilby layer) ― 버프시 마찰열에 의해 발생하는 용융 유동에 의해 밀려서 생긴 광택면
1>연마면의 표면조도, 광택도 측정법.
조도측정법
1) stylus법 : 레코드판의 원리로써 바늘을 사용하여 일정 속도로 표면을 긁어서 조도를 측정하며, 기록하는 방법. 2) 광학 조도 : 간섭 현미경(Interference microscope)을 사용하여 광의 조사각도 편차 측정하여 홈의 깊이를 알 수 있음(0.1μ이하 깊이). 3) 전자 현미경(SEM), 투과 전자 현미경(TEM) : SEM은 빛의 반사를 통해 표면을 볼 수 있으며, TEM은 대상물의 내부를 볼 수 있음. 4) 광전(光電) 광택도 기록계 : 한쪽에서 비춰진 빛이 반대편으로 반사되는 정도를 이용하여 광택도 측정에 이용함.
2> 전해연마
1) 정의 어떤 특정한 약품의 용액내에서 피연마체(연마되는 물질)를 양극으로 하고, 적당한 금속을 음극으로하여 전기 화학적으로 거시적 또는 미시적으로 요철을 가진 표면을 광택이 있는 평활면으로 만드는 방법
2) 내용 ·전해 연마만으로는 광택이 있는 표면만 얻음 ·정밀도, 평활도를 요구하는 부분품에 대해서는 기계에 의한 예비적 버프 연마를 필요로 한다
V-A curve (전압-전류곡선) 전해연마액 중에 금속을 넣고 직류전압을 가해서 전압을 상승시켰을 때 일반적으로 아래와 같은 전류곡선을 얻는다.
1> a : 미진행 단계
; 양극 금속의 용해는 있으나, 연마작용은 전혀 없다.
2> * : 변절점(critical point)
; 양극금속 표면에 연마피막이 형성되기 시작하는 곳. 전압에 대한 전류가 비례관계가 되지 않는다.
3> b : 양극 금속 용해 효율적으로 이루어짐
; 평탄한 부분이 나타나지만, 이것은 조건에 따라서는 나타나지 않을 때도 있다. 액의 농도가 적을수록 폭이 좁으며, 교반을 하면 더욱 좁아진다. 또한 이점에서 전류밀도도 농도와 관계가 있으며, 진할수록 전류밀도가 낮게 되는 경향이 있다. 그리고, 양극금속은 용해가 효율적으로 이루어 지며, 금속의 종류에 따라서 전해평활화가 되는 수도 있다.
4> c : 연마 및 광택(가스 발생과 양극 용해)
; 가스의 발생이 심해지면서, 전류는 급격히 상승한다. 전해연마면은 평활 할뿐만 아니라, 광택까지 생겨야 하기 때문에 전류밀도는 b-c 사이여야 한다.
5> d : 전해 가공 영역
; c에서 d로의 변환점에서의 전류밀도에서는 귀(바리)를 떼어내는 데 적합하며, 연마작용보다는 가공능(전해가공)의 초단계에 속하며, 이 조전압 이상에서는 완전히 전해가공의 영역이 된다.
Barrel 연마
통속에 물품만, 또는 연마석이나, 윤활제인 용액을 장입하여, 회전시켜 장입물상호의 충돌, 마찰 등에 의해 각을 둥글게 하며, 표면을 갈아 광택을 내는 연마로서, 비교적 소형제품을 대량 연마하는데 쓰여지는 방법이다.
2> 화학연마
1) 정의 화학약품중에 침지해서 화학반응을 촉진시킴으로써, 피연마체를 평활하게 하는 방법으로 그 특징으로서는 산세에서는 주로 산화물의 제거라는 한정된 역할인데 대하여, 이 방법은 소지와 산화물 제거의 양쪽을 겸한 것이다.
2) 내용 ·전압이나 전류대신 산의 농도나 산화제의 종류 등이 중요한 조건이 된다 ·각 부분에서 연마되는 것이 균일하다.(균일성 우수) ·조작이 간단하며 불균일성이 적다
2.2 탈지(Cleaning, Degreesing)
금속표면의 산화물이나, 금속염이외의 오염물을 제거하는 조작을 말한다. 도금준비 작업으로써, 탈지는 가장 중요한 조작이며, 탈지가 불충분하면, 밀착불량, 광택불량, 거친 도금, 피트, 부풀음, 최성등의 불량원인이 된다.
2.2.1 정의
― 금속 표면의 산화물이나 금속염 등 오염물을 제거하는 방법 ― 탈지가 불충분하면 밀착 불량, 광택 불량, 거친 도금, 피로, 부풀음, 취성 등이 발생한다
2.2.2 Solvent Degreasing(용제탈지)
유기용제(휘발유, 석유, 트리클로로 에틸렌 등)로 오염물을 용해 제거하는 방법이며, 도금전처리로 완전치는 못하며, 예비탈지에 속한다.
·C2HCl3 (트리클로로 에틸렌) ― 예비 탈지로만 사용 ― 세척력에 비해 독성이 적으며 용해도가 크고 휘발성이 크다
·KB가(카우리 부탄올 가) ― 유지분 용해력을 비교하는 방법의 하나임, 독성이 있다.
2.2.3 Alkaline cleaning (알칼리 탈지)
유지분을 알카리(가성소다, 탄산소다, 인산소다, 규산소다, 청화소다 등)로 수용성의 비누를 만드는 산화작용에 의해 오물을 제거하는 방법이며, 온도를 높여 반응속도를 크게 하고, 유화작용을 도모하기 위해 소량의 계면활성제를 첨가한다.
·비누화(알칼리+스테아린산) ― 물에 불용성인 기름이 수용성 비누로 변함 ― 검화, 습윤, 침투, 분산, 유화 작용으로 제거
·탈지용 알카리염과 pH(완충 작용)
·경수 봉쇄제 농축된 인산염은 경수 중의 Ca, Mg을 중화시켜서 탈지나 수세 때 전혀 해가 없도록 해주고 있다
·킬레이트 ― 이온 봉쇄 : 킬레이트 제(chelating agent)
2.2.4 전해 탈지(Electrocleaning)
용제탈지, 에멀션탈지,알카리 침지 탈지는 공업적으로 일종의 예비탈지이며, 전해탈지는 마무리 탈지이다. 따라서, 전해탈지는 예비탈지후에 해야 하며, 예비탈지를 생략하거나, 거칠게 하고, 전해탈지에만 의존하는 것은 크게 잘못이다.
1) 정의
전해에 의하여 음극(H2) 또는 양극(O2)에 발생하는 가스의 심한 교반과 금속과 더러움의 중간에 많은 가스가 발생하여 더러움의 신속한 제거가 이루어짐.
*음극 탈지
― 음극에 발생하는 수소에 의한 금속 표면의 환원 ― 분리되는 속도 빠름 ― 수소 발생으로 인한 수소 취성의 우려 ― Ni, Stainless Steel, Al, Brass
수소발생으로 바깥의 산화물층이 제거됨(∵Fe2O3는 전기를 통과시키지 못함)

검은 부분은 절연파괴 현상으로 전류 통함(약한부분 crack발생), 가스가 발생으로 파괴.
*양극 탈지
― 양극에 발생하는 산소에 의한 더러움의 산화 : 철저한 산세가 필요 ― 분리되는 속도 느리다 ― 산화물 생기면 좋지 않다 ― Zn : pH가 낮고 전해시간도 짧게 해야 한다. ― 첨가하는 계면 활성제에는 저기포성의 비이온형이 좋다.
*전해탈지의 장점
1) 전해에 의해서 음극 또는 양극에 발생하는 가스의 심한 교반과 금속과 더러움의 중간에 많은 가스가 발생함으로써, 더러움의 신속한 제거가 된다. 2) 음극탈지일 때는 음극부근에 Na 이온 등의 석출하며 수소가스의 발생과 동시에, 알카리가 생김으로써 강알칼리가 되어 유지의 비누화를 가속시킨다. 3) 음극에 발생하는 수소에 의한 금속표면의 환원. 4) 양극탈지일 때는 양극에 발생하는 산소에 의한 더러움의 산화. 5) 양극용해에 의한 금속표면 화합물 및 더러움의 제거 등의 장점이 있다.
*전해탈지의 단점
1) 음극탈지에서는 음극에 생기는 철강등의 수소취성이 발생 2) 불순물의 흡착 또는 전착. 3) 전기적 불균일성으로 인한 탈지효과의 불균일성 발생 4) 발생하는 가스의 mist공해와 폭발의 위험성 등이다.
2.2.5 에멀션 탈지(Emulsion cleaning)
용제와 물에 계면활성제를 첨가하여 유화시킨 액(유화제)으로 오물을 제거하는 방법이며, 물 10 - 200에 용제 1정도의 계면활성제 0.1 - 0.5% 액을 사용하며, 물에는 알카리를 3 - 10 g/l 가할 수도 있다. 예비탈지에 속한다.
·에멀션 탈지제는 클로로에틸렌, 케로신 등의 용제와 물을 유화시킨 용액 ·침지 또는 분사해서 탈지하거나 수세할 때에 용재화, 기름분을 에멀션으로 만들어 제거함
2.2.6 초음파 탈지
물건을 탈지액(용제 또는 알카리)중에 침지하여, 이것에 초음파의 진동을 주어 공동현상(Cavitation)에 의한 오물제거 능력을 높인 방법인데, 떨어지기 힘든 고형물이나, 구석에 있는 더러움도 쉽게 떨어진다. 그러나, 이 장치는 값이 비싸고, 설계가 잘되어 있지 않으면, 충분한 효과를 얻을 수 없다.
2.3 산처리(Pickling)
도금전처리로서의 산처리에는 산세와 산침지의 두가지가 있다. 이들은 정도의 차이는 있을 망정, 소재금속면에 생긴 산화층을 제거하고 새로운 금속면을 노출시켜서 외관과 밀착성을 향상시키는 처리방법이다.
정의
소재를 열처리나 장기간의 방치로 금속표면에 발생한 산화피막이나 수산화물을 산으로 제거하는 화학적 방법을 말한다.
― 금속 표면의 산화피막, 수산화물을 산으로 세척 ― 대부분 금속 표면 산화 피막은 산세 반응으로 제거 가능
Acid Dip(산침지) : 금속을 산에 단시간 침지하는 처리로 표면 산화층을 제거하여 표면을 활성상태로 만든다.
cf) HCl + H2O →「HCl 이 우선 휘발되므로 점점 묽어진다.」: 상온의 HCl 은 보통 15∼50%로 사용하기도 한다.
H2SO4 + H2O → 점점 강산이 된다. (50∼70℃ 황산 : 10%)
2.3.1 산세 반응(pickling)
<염산에 의한 산세반응>
1) ― Fe + 2HCl → FeCl2 + H2 2) ― FeO + 2HCl → FeCl2 + H2O : 불안정 상으로 고온에서만 존재 3) ― Fe2O3 + 6HCl → 2FeCl3 + 3H2O 4) ― Fe3O4 + 8HCl → FeCl2 + 2FeCl3 + 4H2O
* 위1)식 반응에서 발생하는 수소는 녹이나 스케일을 제거시키는 기계적 작용을 촉진시키는 역할도 하지만, 산화물을 금속으로 환원시키는 역할도 한다.
* 2) - 4) 식은 철강의 산화물을 용해시키는 반응이지만, 능률은 과히 좋지 않다.
* 일반적으로 HCl을 사용하는 경우 HCl의 휘발 때문에 농도를 일정하게 만들기가 어렵다.
* 특히 황산은 스케일을 용해시키는 능력이 적다. 온도를 올리는 것이 효과적이기 때문에 경제적인 효율이 떨어진다.
산소의 반경이 Fe의 반경보다 크다. 부식이 진행되면서 scale 을 밖으로 밀어내므로 벗겨지게 된다.

문제점
1) 산에 의한 소지 용해로 금속표면을 거칠게 하여, 도금의 외관을 손상시킴. (matrix의 Fe성분이 녹아 나옴)→억제제 사용함으로써 소지 용해 방지. 2) smut 현상 발생 (외관 손상) 3) 용해할 때 발생한 수소가스가 소지의 원자사이 빈공간에 들어가 수소 취성야기 (음극 전해 탈지, 산세, 전기 도금 등에 의해 생긴 수소가 금속에 침투하여 부러지거나 깨지기 쉽고 갈라지는 것)
2.3.2 취성 방지(수소취성)
수소취성은 음극전해탈지, 산세, 전기도금 등에 의해서 생긴 수소가 금속 특히 철강제품에 침투함으로써 이로 인해서 부러지거나 깨지기 쉽고, 갈라지는 예도 있다. 이것은 강의 경우 항복강도가 낮은 강철일 때 흡수된 수소가 강의 개재물(介在物) 속에 모여서 이들 수소분자의 압력으로 깨지게 된다. 특히 MnS, Al2O3, SiO2 등의 개재물이 균열의 기점이 된다. 수소취성은 재료의 강도가 클수록 극미량의 수소에 의해서도 취성이 생기며, 孔蝕部位를 기점으로 하여 발생하기 쉽다. 수소가 강철에 침입하는 결로를 보면 수소는 원자 중 가장 작아서(1.06Å) 금속격자(2∼3Å) 사이를 쉽게 원자상태로 뚫고 들어가기 때문이다. 이들 수소취성을 방지하려 할 때는 다음의 몇 가지 방법을 취하면 된다.
① 전해탈지에서는 철강의 경우 양극탈지를 택하도록 한다. ② 산처리를 할 때는 되도록 짧은 시간에 산세하도록 하며 산억제제 (inhibitor등)을 첨가한다. ③ 고탄소강 등 수소취성이 많이 생기는 물건은 산처리 대신 블라스팅 등 기계적 녹제거나 특수 알칼리 탈청방법을 선택한다. ④ 아연도금에서는 산성아연도금이나 특히 메커니컬(mechanical)도금을 하도록 한다. ⑤ 구리도금에서는 시안화구리보다 피로인산구리도금이 가볍게 생긴다.
또한 일단 수소취성이 생기면 다음과 같은 방법으로 수소취성을 제거한다.
⑴ 산세 후 가열된 알칼리용액에 넣어서 침입한 수소를 도금하기 전에 제거한다. ⑵ 200℃정도에서 4시간 가령 베이킹(baking)을 시킨다. 이 베이킹은 금속의 종류, 피막상태, 도금의 종류, 소재의 두께 등에 따라서 다르다. 예를 들어 아연 도금층은 수소가 통과하기 힘들고 같은 아연이라도 광택도금이 또 두께가 두꺼운 도금이면 수소의 방출이 힘들므로 베이킹시간이 길어야 한다.
2.4 수세
수세는 도금할 물건의 표면에 부착되어 있는 도금액의 피막을 단시간에 수세조 내에 확산시키기 위해 필요한 공정이며, 확산을 촉진시키기 위해서 공기교반, 강제대류, 온수수세, 스프레이 수세 등을 하고 있다.
병렬 수세식, 직렬 수세식
도금공정에서 수세조는 보통 3조를 사용하는 경우가 많으며, 이 때 각각의 수조에 따로 따로 물을 공급하는 병렬방법이 있고, 수세하는 물건과는 반대방향으로 물이 흐르는 즉, 최종으로 수세하는 물이 새로 공급되는 물이 되는 직렬역류수세방법(counter flow)과의 두가지 방법이 있다. 직렬 역류 수세방법이 물도 절약되고 따라서 폐수를 줄이는 방법이 된다.
녹 제거
* 산세 : 산 용액에 침지시켜 녹을 용해시킴
* 전해 산세 : 전류를 통하여 발생되는 gas에 의해 녹 제거 : 산용액에서 물건을 양극 또는 음극으로 하여, 3∼10 A/dm 의 전류를 통하여 발생되는 gas에 의해 녹제거의 능률을 높인 것. 별로 실용되지는 않고 있다.
* 전해 알카리 탈청 : 음극 또는 PR로 녹 제거 : 수산화 나트륨, 시안화 나트륨, EDTA, 구루콘산나트륨 등의 알카리 용액에서 50 - 70 C , 10 - 20 A/dm , 음극 또는 PR로 녹을 용해 제거하는 법. : 스머트, 수소취성을 일으키지 않는 것이 장점이다.
* 스머트 : 산세 및 알카리 탈지 후 표면에 남아 있는 검은 물질로써 고 탄소일 때 접착력 저하됨
* 인히비터 + 침식 억제제 [인히비터 : 철소지의 침식을 억제하는 약품.]
2.5 금속 전착
금속 전착 : 전기적으로 Cathode극에 붙는 것. 환원석출이 됨. M+→M (cathode)
양극 현상 : M→M+(anode)
2.5.1 전착 기구
전기 이중층 아래 그림에서와 같이 점선으로 내려 그린 부분은 외측 헬름홀쯔면(OHP)이라고 하는 전극표면에서 가장 가까운 거리이다. 이 지역을 헬름홀쯔층 또는 전기이중층이라고 한다. 전하 M+가 cathode의 M에 가까워짐에 따라 발생한다.
·H2O는 비대칭 구조 dipole 형성

전하 이동 : 전하 M+가 안정한 방향으로 이동 : 전류 밀도, 과전압, 첨가제에 의해 영향을 받는다
물질 이동 : 대류 또는 확산에 의해 영향을 받는다
용액 중 금속 ion + 물 분자 = aquo- ion(수화 이온)
2.5.2 과정
1) 용액 본체에서는 아쿠오이온의 물분자는 등방배치를 하고 있다. 2) 확산에 의해서 아쿠오이온이 음극에 접근하면, 음극부근의 전위구배가 높으므로, 물분자의 배향이 생긴다. 3) 전기이중층을 통과한다. 이 때 물분자의 일부를 떨어뜨린다. 아래 그림에서는 이미 전기이중층의 외측에서 탈수화가 완전히 이루어진 것으로 표현되어 있으나, 실제로는 일부의 물분자를 가진 형태로 금속에 도달하는 것으로 생각된다. 4) 전기이중층을 통과한 이온은 금속표면에 흡착된다.

·용액중에 흡착성이 강한 이종 이온이 있게 되면 → 먼저 활성점에 흡착 → 금속 adion 의 활성점으로의 도달 방해 → 다핵화
2.5.3 제어 Parameter
확산 속도 (금속표면에서) ― 확산 속도가 크면 grain growth : worse ⇒ 조대 성장 ― 확산 속도가 작으면 nucleation : fine ⇒ 표면 평활, 광택
전류 밀도 ― 전류 밀도가 크면 다핵화(多核化) : 표면 도착 adion 증가(많다.) : 활성점의 수도 한정, 불활성한 곳의 성장점을 구하며 다핵화. ― 전류 밀도가 작으면 활성점 이동이 크고 aidon 감소
과전압 ― 과전압이 크면 다핵화 ⇒ 미세화 ⇒ 광택 우수 ― 과전압이 작으면 조대 성장 ⇒ 활성점 이동이 크다
광택제 ― 음극 분극 증대
2.5.4 leveling action(평활 작용)
평활작용은 균일 전착성에 대해 미소균일전착성이라고도 부르며, 소재 표면의 미소요철 또는 홈 등을 메워주며 평활한 표면을 만들어 주는 작용을 말한다. 표면의 미소요철이 가시광선의 파장정도 (0.1㎛) 이하일 때 광택면이 되는 것이지만, 레벨링 작용의 대상이 되는 요철은 적어도 마이크로 단위이므로, 광택제로서 효과가 있는 첨가제가 모두 레벨러로서 우수하다고는 볼 수 없으므로, 레벨러로서 별도로 첨가하는 경우도 있다.

: leveling 작용의 본질은 금속이온의 석출에 대한 방해 물질이 음극상의 볼록부에 우선 흡착 → 그 부분의 과전압을 높이고 → 오목부의 2차 전류밀도 개선
요철이 0.1㎛ 이하( 가시광 파장 이하)
leveler 첨가 ― 티오요스, 사카린
leveler 작용 기구 : leveler 분자 또는 ion 은 음극표면의 볼록부에서 많이 석출하며 그 부분의 과전압을 증대 → 오목부의 전류밀도가 높아짐 → 도금층 두께 증가 → 소지표면의 요철 평균화 : 음극 분극 증대 : leveler 음극 석출은 diffusion rate controll : leveler → 2차 전류 밀도 개선 : leveler 의 확산층 두께는 음극표면의 볼록부에서는 엷고 오목부에서는 두껍다. (δ1 < δ2)
2.5.5 착 이온 전착
1) 착염욕으로부터의 전착은 단순염욕으로부터 보다는 높은 과전압하에서 이루어지기 때문에 미립자이며, 밀도가 높은 석출물을 얻기가 쉽다. (밀착이 좋다.) 2) 단순염욕에 비해서, 균일전착성이 우수하다. 3) 균일전착성이 좋은 대신 레벨링이 좋은 전착물은 얻기 힘들다. 4) 착염욕에서 도금하면 단순염욕에서는 불가능했던 합금도금이 가능하다. 5) 거의 모든 금속은 알칼리성에서는 난용성의 수산화물을 얻게 되는데, 착염화시킴으로써 알칼리성에서 가용성 물질이 된다.
2.5.6 결정 성장 인자
전류 밀도 이온농도에 비해 전류밀도가 낮으면, 핵수가 적으므로 결정은 잘 발달하며, 전류밀도가 증가할수록 결정은 작아진다.
ion 농도 금속 이온농도가 작을수록 가수분해가 생기기 쉽고 콜로이드 상의 수산화물에 의해서 2차적으로 저지작용이 생기며, 이 작용이 강하면, 핵생성이 강하여, 결정립이 곱게 되며, 약하면, 핵생성도 약하여, 입자는 크게 된다. 전애액 중에 목적금속 이온 농도가 작고 이온을 보급하는 원자단은 액 중에 대량 존재할 필요가 있다.
·단순염 일 때 이온 농도를 작게 → 한계전류밀도가 낮아져 도금이 잘 안됨. 따라서 농후한 액을 사용하여 전류 밀도를 크게, 첨가제 첨가 → 핵을 많이 만듬. 성장을 머물게 함.
착염, 첨가제 착염형성제를 첨가하면 금속이온 농도는 극히 작아지므로, 역시 미세한 결정을 얻을 수 있다.
클로이드 물질 첨가
온도
교반
2.6 도금 설비
― D.C 전원, 도금조(전해액), 전극으로 구성되어 있다.
2.6.1 D.C 전원
SCR 정류기 ― 반파 정류(단상 단파) : 교류 전류에서 -전류는 없애고 +전류만 정류한다. ― 전파 정류(단상 전파) : 교류 전류에서 -전류를 +전류로 전환하여 정류한다. 공업적으로 3상 정류를 많이 사용한다
용수 ·이온 교환 수지 짠물을 단물로 만드는데는 이온교환수지를 많이 사용한다. 이것은 일종의 합성수지이며, 이에 결합되어 있는 이온을 물에 있는 다른 이온과 교환하는 역할을 한다. 그리고 재생하여 사용할 수 있다.
― H형 양 이온 교환 수지 (묽은 염산에 의해서) Rㆍ2H + Ca(HCO3) → RㆍCa + 2H2CO3 Rㆍ2H + MgSO4 → RㆍMg + H2SO4 ― OH형 음 이온 교환 수지 (가성소다에 의해서) R′ㆍ2OH + H2SO4 → R′ㆍSO4 +2H2O R′ㆍ2OH + 2H2CO3→ R′ㆍCO3+2H20
·재생 ― 양 이온 수지 RㆍCa + 2HCl → Rㆍ2H + CaCl2 ― 음이온 수지 R′ㆍSO4 + NaOH → R′ㆍ2OH + Na2SO4
2.6.2 도금액 정화
1) 약 전해에 의한 불순물 제거 어떤 도금에서나 되는 것이 아니고 원칙적으로 도금하려는 금속의 석출전압보다 낮은 전압으로 석출하는 금속만이 제거되게 하는 것이다.
: 목적 금속보다 더 낮은 전압으로 불순물을 먼저 전해 시킴 : 도금액 중에서 Zn, Cu가 함께 있을 때 Zn을 석출하려고 할 때 전해 석출을 하면 Cu가 먼저 석출하기 때문에 약 전해에서 우선 Cu를 석출한 다음 목적 금속 Zn을 석출한다
2) 약품 첨가 : 분순물과 착이온 형성하여 가라앉음 : 활성탄 첨가 (예 : 숯)
3) 양극 주머니 : 물리적 화합물 제거 방법 : 떨어지는 비금속 개재물을 걸러준다 : 도금 성질 향상시킴
2.6.3 바렐(barrel)도금기
― 소형 물건을 다량 처리
장점 ― racking 불필요 ― 장입.배출이 자동 ― 연속 조업 가능
단점 ― 소형 제품(500 g 이하) ― 전류 밀도 적음 : 두꺼운 도금에서 시간이 많이 걸림 ― 두께 균일성 부족 ― 액 조성 변동 크다 ― 고 전압 필요 ― 도금액 소모가 많다 ― 너무 적고 엷은 물건은 가벼워서 전기적 접촉이 좋지 않다.
종류 - 편심바렐 : 물건의 혼합이 좋아서 편편한 물건을 도금 할때, 서로 붙는 경향이 적고, 아연 크로메이트 처리등에 적합하다.
- 요동식 바렐 : 도금액의 농도 변화가 적고 도금 속도가 빠르다.
- 수평식 바렐

표면 처리는 사용 목적,모재의 종류,모재의 정도,모재의 크기등 여러 가지 요인에 의하여 적합한 표면 처리 방식을 찾아야 한다. 오히려 비싸게 표면 처리를 하고나서 싼방법의 표면 처리 방법보다 못한 결과를 얻을 수도 있기 때문이다.
3.표면처리 표면확산:표면경화;침탄,질화 고주파 소입 화성처리;산화피막처리 인산염처리 기타;금속침투법 이온주입법 피막;습식;전기도금 화학도금 용융염법 건식;CVD(CHENICAL VAPORIZED DEPOSITION);CVD PLASMA CVD PVD(PHYSICAL VAPORIZED DEPOSITION);진공증착 SPUTTERING ION PLATING 기타;분체도장 용사(SPRAYING COATING) 등의 종류가 있으며 주요한 몇가지에 대하여만 간략한 설명을 하고자 함.
3-1.CVD. COATING온도 조건이 약 1,100도가지 올라가므로 오로지 초경의 COATING에만 사용한다. 고온에서 COATING을 하므로 모재와 피막의 열팽창계수의 차이로 표면의 피막이 crack이 갈 수 있으므로 TiC르 기저층으로 하여 통상 다층 COATING을 하여 이를 방지한다.따라서 PVD에 비해 상대적으로 피막의 두께가 두껍다. 부산물로 염산가스가 추출되어 공해의 원인이 된다. 가스가 골고루 침투하여 내경등의 COATING에도 적합. PVD에 비해 COST가 저렴하다. SHARP한 날에는 COATING이 부적절하며 조도가 상당히 거칠게 나온다. 3-2.PVD. CVD보다 낮은 온도인 450도 부근에서 작업하며 최저 180도에서도 작업이 가능 하므로 초경이나 STEEL,PALSTIC,도자기등에 까지도 COATING이 가능. 공해가 없다.막의 두께가 상대적으로 얇다.다라서 정밀한 제품에 맞으며 SHARP 한 날에도 거의 완벽하게 나오며 가공한 면조도 그대로 심지어 가공 WHEEL자욱 까지 그대로 나온다.막의 두께는 내마모용의 경우 편측으로 1-3.5미크론이나 DECORATION COATING의 경우는 1미크론이하로 COATING을 하며 공구의 경우에는 통상 2.5미크론으로 한다. 내경의 COATING은 막힌 구멍의 경우 통상 DIAMETER 경의 깊이(예;경이 5mm이면 깊이 5mm까지)까지는 COATING이 유효한 것으로 보며 터진 구멍의 경우는 경*2의 깊이 이상으로 COATING이 유효하다. COATING시는 제품간에 이격거리를 두어야 하므로 CVD보다 COST가 비싸다. 공구나 금형의 경우 초경은 상관없으나 STEEL인 경우에는 반드시 고온 TEMPERING 된 제품을 의뢰하여야하며 표면은 다른 표면처리(예를들어 흑염처리나 질화처리 가 되어 있지 않아야 하며 EDM(ELECTRIC DISCHARGE MACHINE)작업등을 하였다면 표면 경화된 부분을 제거한 후에 COATING을 하여야 한다. 제품의 표면에 생긴 녹을 제거하여야 함은 물론이다. 3-2-1.진공증착 BOAT(용기)내에서 전자 BEAM이나,유도,저항가열등으로 용해증발시켜 피막을 입히는 방법으로 주로 피막과 모재의 밀착성을 중요시하지 않는 DECORATION COATING이나 전자 부품등의 COATING에 사용하며 COST가 상당히 저렴하다. 3-2-2.SPUTTERING :이온화된 불활성 기체가 타겟 표면에 충돌하므로써 증착 물질을 직접 기화시킴으로 이루어진다. 불활성 기체의 이온화작용은 비평형방전(abnomal glow discharge)영역에서 이루어지며 이온화된 기체는 전기장의 영향에 의해 음극(cathod)표면을 가격 하게됨. sputtering법은 타겟을 음극으로 사용하며 진공기나 모재를 양극으로 한다. 종류로는 RF sputtering법,반응성 sputtering법,..등이 있다. 3-2-3.ION PLATING
;PVD방법 중 가장 발전된 방법으로 HCD(HOLLOW CATHODE DISCHARGE)방식,MULTI-ARC법등 여러 방식이 있다. 피도금체를 음극으로 증발원을 양극으로 한다. 3-2-3-1.HCD(hollow cathod discharge)법; 중공 열음극의 의미로 HCD GUN을 가지고 저전압(수십V), 대전류(300-600A)의 전자빔으로 금속을 용해,증발 시킴 과 동시에 고밀도의 전자에 의해서 증발금속을 효율적으로 이온화(이온화율20-40%)시켜,용이하게 화합물을 생성시킬 수 있는 것이 장점이다. 증발금속이 고체상태에서 용융상태를 지나 기화,이온화 하기 때문에 공구모재의 표면을 손상시키지 않고 치밀한 막을 얻을 수 있다. 3-2-3-2.MULTI-ARC법; 증발원을 음극,진공용기를 양극으로하여 이사이에 직류를 흘려 진공중에 아크방전을 일으켜 금속원소의 프라즈마를 발생 시킨다. 증발원의 표면에 대전류(100,000- 10,000,000A)의 아크 스폿트가 발생하여 음극금속의 증발과 동시에 이온화 하여 이온화율이 50%로 높아서 증발속도가 빠르고 증발원의 소비량도 적다. 수십미크론의 코팅도 가능. 피막이 약간 거칠지만 밀착성이 높은 피막이 얻어진다. 3-2-3-3.반응성 IP법; HCD GUN을 사용하여 저전압,저전류로 증발원을 용해 시키기 때문에 진공용기 외부에 설치된 접속코일로 Ar 프라즈마 를 콘트롤하여 코팅.
3-2-4.각종 막의 종류 TiN; 가장 보편적인 COATING막으로 일반적임. TiCN;TiN보다 내마모성이 우수하며 PRESS금형의 COATING으로 TiC와 함께 널리 사용. 절삭공구에서도 사용. TiALN;고온에서의 AL의 산화로 인한 막을 형성하므로 절삭공구의 고속 절삭용 공구에 알맞는 COATING.저속,저온 작업인 금형에는 적합치 않음. CrN;단순 SLIDING이 되는 부분의 마모에 적합함. DLC(diamdond like carbon);피삭재가 비철 계통인 곳에 사용하나 아직 타발 금형이나 절삭공구에는 시기 상조임.
*참고;1.TD(TOYOTA DEFUSION)에 대하여 대기중에서 고온으로 유지된 용융염욕 중에 철강이나 초경합금등의 재료를 침지 유지함으로 탄화물을 형성시킴과 동시에 모재에 담금질 경화를 하는 PROCESS로서, CVD나 PVD에 그영역을 많이 내준 TD도 나름대로의 장점이 있어 절삭공구에는 사용이 거의 불가능 하지만 금형에서는 오히려 나은 점도 있어 활용되고 있으나 CVD나 PVD에 비한다면 활용범위가 넓지는 못하다. 막자체의 강도는 CVD나 PVD에 비해 우수하나 밀착성이 떨어지어 막이 한번 탈피 되면 그곳을 기점으로 쉽게 막이 벗겨져 나간다. 또한 SHARP한 날의 COATING에는 부적절하다. 1-1.TD의 공정; 염욕가열로에서 800-1500도씨로 유지된 용융염욕 속에 0.5-10시간 침지 유지 함으로 탄화물을 형성한다. 담금질 후 템퍼링을 한 후 부착된 salt(염)을 세정으로 제거한다. 1-2.TD의 특징; 1)피복층의 형성과 동시에 모재의 담금질이 가능하다. 2)마스킹등으로 국부피복이 가능하다. 3)재처리가 가능하다. 4)형상에 관계없이 피복이 균일하며 작은 구멍(0.5mm)이라도 가능 5)모재의 면조도가 거의 그대로 유지된다. 6)탄화물층의 두께를 쉽게 조정할 수 있다. 7)모재 재질에 관계없이 층의 품질이 일정하다. 1-3.TD의 주의할 점; 담금질에 의한 변형과 치수 변화를 주의하여야 하며, 왜곡방지및 균열방지를 위하여 모따기를 해주어야 한다. 처리전의 면조도는 가능한 좋게 하여야 한다. 방전 가공한 제품은 미세 크랙이 있을 수 있는 백색층을 반드시 연마하여 주어야 한다.(균열의 원인이 됨) 치수가 정밀한 제품은 TD 처리 후 연마할 수 있는 여유를 0.2mm 정도 주도록 한다.(통상 편측 10 micro) TD이외의 표면처리층은 완전히 제거하여 준다.
2.용사(SPRAYING COATING) 2-1.용사란? COATING시키고자하는 재료를 열에 의하여 용융시켜 미세한 입자 형태를 빠른 속도로 가속하여 모재표면에 접착시키는 기술. 2-2.용사의 종류. 1)가연성연소의 열원을 이용한 용사 WIRE METALIZING GUN. POWDER SPRAY GUN. D-GUN(폭발용사) HVOF(J-GUN) 2)전기 ARC 열원을 이용한 용사 WIRE METALIZING GUN. PLASMA SPRAY GUN. 3)기타 LASER를 이용한 용사 4)최근의 용사장치 ㄱ)J-GUN;용사화염속도2,100m/sec (cf:D-GUN=1,500m/sec.기타=150m/sec) ㄴ)PAZ JET;용사기 출력250KW(기존80KW) 용사화염속도3,000m/sec(cf;기존=760m/sec) 2-3.용사의 특징. 1)적용의 다양성;적용재료 약200여종,적용대상 재료는 거의 모든 재료에 COATING 이 가능(나무,콘크리트,유리에 까지도.) 2)모재에 열영향을 주지 않으므로 치수변형,모재 성분 변화가 전혀 없음. 3)피막 두께 조정 용이. 4)부분,선택 적용이 가능함. 5)여러 열악한 작업환경에 적용할 수 있는 복합 재료의 복합 COATING이 가능. 2-4.용사가 적용되는 분야. 마찰에 의한 표면 훼손시. 열과 산화에 의한 표면 훼손시. 대기,침수 부식에 의한 표면훼손시. 전기전도 또는 차폐가 필요시. 육성및 보수가 필요시. 화학적 침,부식에 의한 표면 훼손시.
3.TEFLON
3-1.TEFLON COATING이란?
TEFLON(불소수지)을 도료화하여 철, 스테인레스, 알미늄, 동, 유리, 고무, 세라믹, 플라스틱 등 기존 재료에 스프레이(SPRAY)및 분말정전도장, 건조, 가열, 소성의 공정으로 비접착성(이형성)·내열성·내약품성·내마모성·전기절연성등 테프론 고유의 특성을 이용한 우수한 불소수지 도장을 말한다.
3-2.TEFLON의 종류
3-2-1.TEFLON PTFE
비점착성으로 보통 Primer와 Top코팅으로 피막을 형성한다. 이들 제품은 어떤 탄화불소코팅보다 높은 내열성(290℃/550℉)을 보여준다. 또한 매우 낮은 마찰계수, 우수한 내마모성, 내화학성 그리고 내부식성을 보여준다.
3-2-2.TEFLON FEP
비점착성 코팅이며 소결시 유동성을 지닌 물질로 변하기 때문에 무공질의 피막을 형성시켜 준다. 탁월한 내화학성, 내부식성 그리고 우수한 내마모성과 매우 낮은 마찰계수를 보여준다. 최고 사용온도는 250℃(400℉)
3-2-3.TEFLON PEA
분체도장용 제품으로 마무리 공정의 비점착성은 탁월하다. 특히 내화학성과 내부식성이 우수하며 내마모성도 지닌 제품이다. 이러한 특성은 최고 260℃(550℉)이내에서 사용할 때 유지된다. 일반적으로 1차Primer코팅을 해야하며 피막 두께는 10~2000u마이크로미터(5~30mil)까지 가능하다. 분체 도장용 제품으로(150℃/300℉)정도의 내열성과 뛰어난 내화학성 그리고 내부식성을 보인다. 피막두께는 50~2000u마이크로미터(30mil)이상도 가능하다.
3-2-4.SILVER-STON
DUPONT社가 오랫동안 축적된 기술로 개발하여 조리기구용 코팅제로 전세계적으로 널리 사용되며, 우수한 비점착성 및 내구성 그리고 288℃라는 높은 내열온도를 가진 우수한 코팅 피막을 얻을수 있고 1차, 2차, 3차의 시스템 공법으로 소결온도는 약420℃이상에서 처리된다.
3-2-5TEFZEL-S.
비점착성 코팅이며 탄화불소수지에 특수 고분자 수지 또는 변성체를 결합시켜 내마모성을 개선시킨 제품이다. 소결시 피막이 층을 이루며 형성되기 때문에, 낮은 마찰계수, 비점착성등과 같은 일반적인 탄화불소막의 성질을 보지하며 내마모성은 탁월하다. 소성온도는 165℃에서 315℃까지 다양하다. (325℉에서 600℉까지) 이 제품은 1회용 코팅으로도 사용될 수 있으며 부드럽고 청결하며 코팅 처리되지 않은 물질에도 사용될 수 있다. 3-3.TEFLON COATING의 특징
3-3-1.비점착성
TEFLON에는 거의 모든 물질이 달라붙지 않는다.
3-3-2.저마찰 계수
TEFLON의 마찰계수는 부하, 미끄러짐의 속도, 사용된 TEFLON의 종류에 따라 약 0.05~0.20의 범위이다.
3-3-3.비유성
TEFLON의 코팅 표면에는 물이나 기름이 잘 묻지 않기 때문에 청소가 용이하고 많은 경우 자동적으로 청결이 유지된다.
3-3-4.저온도 내구력
대부분의 TEFLON 코팅은 극히 낮은 온도에서도 그 물리적 특성이 변치 않고 유지된다. TEFLON은 영하 270℃의 낮은 온도에서의 사용도 고려될 수 있다.
3-3-5내열성
260℃(400℉)미만에서는 PTFE의 분해는 불가능하다. 205℃~290℃사이(400F~550F)에서의 분해는 미미한 정도여서 특별한 주의가 필요없고 290℃~310℃(550℉~600℉)에서는 간헐적인 사용이 가능하다.
3-3-6.전기적 특성
TEFLON은 광역의 주파수대에 걸쳐 매우 높은 절연성, 낮은 손실률, 그리고 우수한 표면저항률을 보인다. 특별한 기술에 의해 TEFLON은 정전기 방지목적의 도전성 코팅에도 사용되고 있다.
3-3-7.내화학성
일반적으로 TEFLON은 화학적 환경에 거의 영향을 받지 않으며, 높은 내열성과 어떤 강한 산, 알칼리 그리고 용제에도 견딜수 있는 제품으로 불소수지계의 다양한 재질로서 귀사 화학공정의 특성에 맞게 효율적으로 시공하고 있습니다.
3-4.TEFLON의 적용예
3-5.TEFRON COATING의 공정
3.염욕 질화 침탄법
3-1.개요:
염욕 질화-침탄법은 강(steel), 주철(castiron),그리고 소결재료(sintered ironmaterial)로 만들어진 공작물의 피로강도 뿐만 아니라 마모와 부식에 대한 저항력을 키우기 위하여 사용된다. 많은 경우 염욕 질화-침탄법은 동등하거나 더 우수한 품질과 매우 우수한 경제성으로 인하여 케이스 하드닝(case hardening)과 하드 크롬 플레이팅(hard chrome plating)등의 다른 표면 처리과정에 대한 대안으로 사용된다. 부식에 대한 저항력은 질화-팀탄법 과정에서 생성된 복합물층(compound layer)을 산화 염욕 처리를 함으로써 더욱 강화될 수 있다. 만약 처리가 된 요소가 다른 무른 재질과 짝을 이뤄야 한다면, 래핑(lapping),연마(polishing), 유리구슬 피닝(glass bead peening), 진동 연마(vibratory polishing)또는 다른 방법을 이용해서 요구되는 수준으로 표면조도를 맞춰야 할 필요가 있다. 기계적인 연마(polishing)후에 산화 염욕에 다시 담그는 것은 합금하지 않았거나 저수준의 함금 강(steel) 으로 이루어진 부푸에 검푸르게 빛나는 표면을 형성하게 되고 이 표면은 많은 경우 갈바닉 프로세스(galvanic porcess)또는 화학적 프로세스를 거친 표면보다 뛰어난 내 부식성을 갖는다. 작업은 염욕 질화-침탄법, 산화냉각, 기계적인 연마(polishing),래핑 또는 진동을 통한 피니싱(vibratory finishing),그리고 산화 염욕조에 다시 살짝 담그는 순서의 프로세스로 이루어진다. 염욕 질화-침탄법은 섭씨 580도에서 이루어진다.녹은 염(salt melt)은 시안염(alkali cyaNate)과 탄산염(alkali carbonate)으로 구성된다. 프로세스는 통기장치(aeration device)가 달려있고 특별한 물질로 만들어진 용기 내에서 이루어진다. 질화-침탄법 과정 중에 철 성분의 표면과 녹은 염 사이에서 반응이 일어나서 탄산염이 형성된다. 염욕의 재생성 과정중에 탄산염은 활성화된 시안염으로 바뀐다. 이러한 목적을 위하여 탄소, 질소, 그리고 수소의 유기 화합물로 이루어진 플라스틱 타입의 재생성자(regenertor)가 사용된다. 재생성자는 염욕의 부피를 증가시키지는 않는다. 그림 1은 예전 프로세스의 차이점을 개략적으로 보여준다. 질화-침탄법 염욕의 재생성 과정중에 부피의 증가가 없기 때문에, 염(salt)을 펴낼 필요는 없다.
그림1 : Reaction duning nitrocatburzing and comparison between the old and new non pollution process
염욕 질화-침탄법 과정 후에 이루어지는 산화 처리과정(oxidative treatment)은 AB 1 냉각조에서 행해진다. 이 냉각조는 새로운 프로세스를 위하여 개발된 것이다. 냉각조의 역할 중 한가지는 질화-침탄법 과정중에 생성되는 미소량의 시안화물과 시안념을 제거하는 것이다. 이 과정을 통해서 공작물을 세척하기 전에 공작물에 붙어있는 유해물질이 확실히 제거된다. AB1 냉각조는 섭씨 330~400도에서 작동된다. 냉각조 프로세스는 유해물질과 그것의 산화 영향력을 제거하는 것 뿐만 아니라 냉각된 공작물의 치수를 안정화시키는 작용도 한다. 실제 현장에서의 반복되는 경험이 이러한 사실을 증명한다. 그림 2는 시안화물과 시안염에 대한 제독 성능과 냉각조 온도 및 반응시간의 관계를 보여준다. 이것은 냉각조에 다량의 액체 질화 염욕을 부어넣은 가혹조건에서 실험을 한 결과이다.추천하는 온도하에서 잠깐만 냉각조 과정을 거쳐도 시안화물과 시안염이 완전히 제거된다.
그림2 : Decompoition of cyanide and cyanate in the AB1 bath in relation to temperature and immersion time
프로세스는 간단한 과정이다.
염욕 처리과정에서 일반적으로 행하듯 공작물을 먼저 공기중에서 대략 섭씨 350도로 가열한다. 그 후에는 섭씨 580도 하에서 보통 30~120분 프로세스를 거치다. 섭씨 330~400도의 AB 1 냉각조 프로세스를 거친다. 공작물의 냉각조의 온도까지 냉각될 때까지 AB 1 냉각조에 넣어둔다. 이것은 대략 10~15분이 소요된다(그림3의 프로세스과정 I). 세척과 클리닝 작업이 뒤따르게 된다. 만약 질화-침탄법 과정을 거친 후 공작물의 표면이 어떤 용도로 사용되기에 너무 거칠다면 후에 설명할 적절한 기계적 방법에 의하여 매끄럽게 만들 수 있다. 그러나 이러한 후 처리 과정은 염욕 질화-침탄법 과정과 산화 냉각과정에서 얻어진 내부식성을 일부 감소시킨다. 그러므로 AB 1 냉각조에서의 산화 처리과정은 기계적인 후처리 과정후에 행한다. 이 과정이 그림3의 프로세스 과정 II를 이루게 되며 지금까지의 모든 과정이 프로세스를 이루는 것이다.
그림3: Process sequence
3-2.특징;치수변화 및 형상 변형 없음.(열처리 어려운 엷고 긴 부품 처리가능) 내마모성 및 피로강도의 증가. (표면 세라믹 코팅처리) 내식성이 우수함.(스텐레스 대체가능) 3-3.적용사례; 습기, 대기에 노출되는 부품의 내식성과 내마모성을 향상시키기 위한 경우 상호 마찰에 의해 쉽게 마모되는 마찰부품의 내마모성을 요하는 경우 내열 환경에서의 내마모성을 향상시키기 위한 경우 마찰에 의한 소착 상태를 개선시키기 위한 경우 동력 전달용 회전기구부품(기어,캠, 롤러등) 의 내마모성과 반복피로 강도를 향상시키기 위한 경우
처리 제품 샘플
3-4.내마모성 복합물층(compiund layer)의 합금적 구조(intermetalic stucture)는 마찰과 다른 금속 부품과 눌어붙는 경향(tendency to weld)를 감소시킨다.질화-침법 과정을 거친 요소들은 매우 우수한 스라이딩 특성과 사용특성, 그리고 매우 높은 내마모성을 가진 것으로 잘 알려져 있다. 질화-침탄법 처리를 거친 부품들은 마모성 테스트나 일상적인 사용에서 모두 일반 표면 경화처리보다 훨씬 우수함을 확인시켜주었다. 하드 크롬 플레이팅 레이어와의 비교에서도 복합물층의 우수함이 드러났다. 변속기 축(transmission shaft), 플러그게이지(plug gauges), 유압 계통 부품 등의 실제적인 응용예에 질화-침탄법 프로세스를 거친 요소들을 사용한 결과 하드 크롬 플레이팅 처리된 부품에 비하여 더 긴 수명을 보였다. 산화처리(oxidative treatment)를 통하여 복합물층의 내마모성을 한층 더 높일 수 있음이 실험실에서의 테스트나 실제적인 사용에서 나타났다. 질화-침탄법 처리에 관련하여 확산층(diffusion layer)의 내마모성에 대한 질문이 종종 제기되었다. 그림 12는 다양한 열처리를 거친 로커 암(rocker arm)들을 냉간 주철로 만들고 질화-침탄법 처리를 한 캠축과 함께 구동시킨 후 접촉면에서의 마모를 비교한 결과를 보여준다. 비록 케이스 하드닝 처리를 한 로커 암의 표면경도가 질화-침탄법 과정으로 인하여 조금 줄어들었지만, 내마모성은 약 80시간이나 증가하였음이 확연히 드러난다. 70~80시간 경과 후, 마모곡선이 케이스 하드닝 처리만 거친 로커암과 평행하게 진행함은 복합물 층이 없기 때문인 것으로 설명된다. 이 예는 복합물층이 제거된 경우에라도 자발적으로 마모가 일어나는 위험성은 없음을 보여주는 것이다.
재질 선택의 적합성은 각각의 마모 메커니즘에 의존한다. 점착 마모(adhesive wear) 를 방지하려면 질화-침탄법 처리를 거친 부품이 다른 표면처리를 거친 부품보다 상대 부품을 훨씬 적게 마모시키기 때문에 접촉 상대 부품으로 선택하는 것이 아주 좋음이 증명되었다. 그림 13은 다양한 재질로 만들어진 기어의 마모 하중 한계(scuffing load limit)를 보여준다. (Niemann Retting)그것은 기어 이빨에 토크를 가하여 마손이 일어날 때까지 토크를 증가시켜 얻은 결과이다. 18%의 크롬과 8%의 니켈을 함유한 오스테나이트 스틸이 가장 낮은 마손 저항성을 갖고 있었으나 질화-침탄법 처리를 통하여 마손 하중한계치가 2~5배로 증가되었다.
내마모성과 사용 특성에 관련하여 또 하나의 흥미로운 요소는 표면의 마찰계수이다. 슬라이딩중에 발생하는 면과 면 사이의 반응은 상대 부품의 절대 경도에는 크게 의존하지 않고, 상호 재질의 선택,구성, 구조, 표면의 기하형상, 그리고 윤활재에 의존한다. 우리는 표면층과 윤활재에 관련하여 다양한 짝에 대하여 표면 마찰 계수를 평가하기 위하여 앰슬러 테스트(Amsler test)를 실시하였다. 앰슬러 테스트란 두장의 디스크를 수직으로 쌓아놓고 위의 디스크는 정지상태를 유지하고, 아래의 디스크를 200rpm으로 회전시키는 것이다. 하중은 점착 마모를 방지하기 위하여 5~30N으로 제한된다. 더 큰 하중을 가하면 마찰계수도 증가하지만 5~30N의 범위에서는 일정한 값을 유지한다. 그림 14는 다양한 짝에 대하여 윤활재 없이 실험한 경우와 SAE30오일로 윤활시킨 경우를 보여준다. 실험이 끝난후 하드 크롬 플레이팅처리, 케이스 하드닝 처리,질화-침탄법 처리 후 물을 이용한 냉각 또는 AB 1냉각조에서으 냉각처리를 거친 샘플 모두 4㎛의 표면조도를 갖게 되었다. 단지 처리를 거친 샘플만이 등금 360과 600의 금강사와 동등한 R=1㎛의 표면조도로 낮아졌다.
윤활재없이 실험한 경우엔 질화-침탄법 처리를 거친 샘플이 케이스 하드닝 또는 하드 크롬 플레이팅 처리한 샘플보다 확연히 낮은 마찰계수를 보였다. 질화-침탄법 처리를 한 샘플은 복합물층의 산화처리를 하면 할수록 표면의 마찰계수가 증가하였다. 윤활시키며 실험한 경우에는 필름에 인가된 유체역학적 하중을 고려해야만 한다. 앞에서 설명했듯이 낮은 표면조도를 가진 염욕질화침탄 샘플만 제외하고 다른 샘플들은 표면의 미세한 봉우리들이 윤활을 방해하기 때문에 윤활재가 있는 경우와 없는 경우의 중간적인 특성을 보인다. 윤활을 시킨 후 ceramicrixe 처리를 거친 샘플이 다른 모든 것들에 비하여 낮은 마찰계수를 갖고 있었다.
3-5.실제 응용 예 프로세스를 거친 공작물들의 내부식성, 내마모성,그리고 피로 강도를 테스트하기 위하여 다양한 방법이 이용되었다. 이 테스트들이 크롬 플레이팅이나 니켈 플레이팅 또는 다른 표면 층 생성법보다 질화 침탄 프로세스가 우수함을 보여주었다. 그림 17은 자동 공조장치나 승용차의 자동 윈도우에 사용되는 모터의 드라이브 샤프트를 보여주는 데 지금껏 내부식성 강으로 만들어져왔다. 질화 침탄 프로세스로 인하여 값비싼 재질 대신 합금하지 않은 케이스 하드닝 강으로 바꿀 수 있었다. 질화 침탄이 부품에 요구되는 내부식성과 내마모성을 부여한 것이다.다른 재질로 바꿈으로 인하여, 이 부품을 장착하는데 걸리는 시간이 더 짧아졌다. 이 드라이브 샤프트의 기계적인 처리는 진동 폴리슁(vibratory polishing)으로 끝났다.
그림5 : treated drive shafts
GG20으로 만들어진 그림 18의 마찰콘 플렌지(friction cone flnge)는 내마모성과 내부식성을 향상시켜야만 하는데, 2.5시간동안의 질회-침탄법 프로세스와 질화 침탄 프로세스로 인하여 요구되는 특성을 만족시킬 수 있었다. 이 플렌지들의 작동면은 4bar의 압력하에서 직경 40~70㎛의 유리알로 피닝을 해서 마무리 되었다.
그림 19는 SAE 8620으로 만들어서 다양한 단계의 처리를 거친 기어쉬프트 슬리브(gershift sleeves)를 나타낸다. 이 부품은 대량으로 생산되는 콤바인 수확기의 기어링에 들어가는 것이다. 지금까지 사용되어온 크롬 플레이팅 처리법과 비교하여 내부식성과 내마모성의 향상은 상당하다. 처리비용 또한 대략 1/3수준으로 떨어뜨릴 수 있었다. 크롬 플레이팅의 조립라인이 있는 공장에서 함께 이루어져야 했음에 비하여 질화-침탄법 처리법은 외주처리가 가능함을 반드시 고려하기 바란다
그림6:T treated gearshaft sleeves
일본에서는 그림20에 보인 카메라 부품들이 대량으로 처리되고 있다. 60분간의 질화-침탄법 처리,산화냉각, 기계적인 연마(machnical polishing),그리고 다시 산화염욕에 살짝 담금으로써 요구되는 내부식성과 내마모성을 얻을 수 있었다.
그림7:camera parts treated
응용예를 일일이 나열하자면 끝이 없다. 그림 21은 이 처리법이 사용될 수 있는 폭넓은 응용사례들의 일부를 보여준다. 이러한 일상적인 부품들은 자동차 업계, 가재도구 제조업체, 섬유용 기계류, 유압 부품류, 광학장치 그리고 항공기 산업계에 두루 걸쳐 대량생산체제 하에서 처리를 거치는 것들이다.
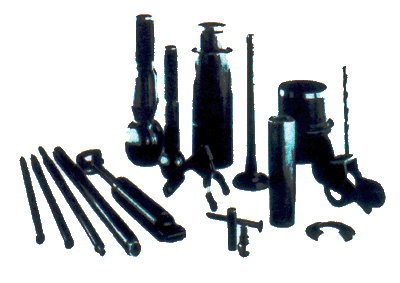
그림8:Various prts treated in mass production
표면 종류 |
특기 사항 |
No.1 |
열간압연, 열처리, Descaling을 한 것. 열간압연 후 열처리하여 Scale을 제거함으로 얻어진다. 일반적으로 공업용 Tank 제작이나 화학공업장치 등 내식성만 중시하고 후판을 사용하는 경우 사용된다.
|
No.2D |
냉간압연 후 열처리 및 Descaling을 하여 얻은 무광택의 냉간 압연 제품이다. Dull Finish 라고도 하며 내식성을 요구하면서 빛의 반사가 요구되지 않는 곳에 사용된다. 일반적으로 Deelp Drawing 성이 양호하나 적은 연신이 일어나는 부위에서는 Stretcher Strain 의 결함이 나타날 수 도 있다.
|
No.2B |
냉각압연 후 열처리 및 Descaling을 한 후 Skin Pass 라는 약간의 냉간압연을 한 제품으로 No. 2D 에 비해 광택과 표면 평탄도가 양호하고 조질압연으로 기계적 성질을 개선하여 Stretcher Strain 의 발생을 제거한 제품이다. 일반용도에 사용되는 대표적인 냉각압연 제품이며 거의 전 용도에 사용된다.
|
No.3 |
KSL6001 (연마재 입도규정) 에 의한 100 ~ 120 MESH 의 연마재로 스테인레스강 표면을 연마한 제품이다. 건축내외장재, 각종 전자제품외관, 주방설비 등의 광범위한 용도로 이용되고 있다.
|
No.4 |
KSL6001 (연마재 입도규정) 에 의한 150 ~ 180 MESH 의 연마재로 연마한 제품이다. No. 3 제품보다 연마상태가 미세하고 은백색의 미려한 표면을 갖고 있으며 욕조, 건축내외장, 식품설비 등에 사용된다.
|
No.6 |
No. 4 제품보다 연마상태가 더욱 미세한 Satin Finish 제품이다. 이는 Tampico Brush 나 Scotch Brite로 약하게 연마하여 광택을 제거한 우아한 표면상태를 띠며, 고도의 반사광택면과 Contrast 효과를 위한 건축재에 이용된다.
|
표면 종류 |
특기 사항 |
No. 7 |
어느 정도의 반사기능을 가진 제품으로 400 ~ 600 MESH 이상의 연마재로 Buff를 회전시켜 연마하여 만들어진다. 연마흔적은 완전히 제거되지 않는다. 주로 우유 및 식품의 낙농산업용 Tank 설비 및 건축자재 장식 또는 공업용으로도 이용된다.
|
No. 8 |
상당한 광택 및 반사기능을 가진 연마제품으로 800 MESH 이상의 연마재로 Buff를 회전시켜 연마하며 연마흔적이 거의 없는 것이 기준이나 실용상 연마 정도에 따라 생산 Cost 및 생산방식이 차이가 없어 한도견본에 의해 생산되며, 주 용도는 건축용 SASH, No.7 제품의 용도와 유사하다.
|
8K (Mirror) |
Buff 방식이 아닌 Lapping 방식으로 5,000 MESH 정도의 연마재를 양모로써 연마하여 거울과 동일한 광택과 연마흔적을 전혀 남기지 않는 고광택 제품을 의미한다. 주 용도는 반사경, 인쇄용 Press판, 가구장식, 건축내외장재로 폭넓게 사용된다.
|
Hair Line |
No.4 제품에 적당한 입도의 연마재를 사용하여 연속된 연마흔적이 나타나도록 한 제품이다. 연마흔적의 연속으로 인하여 국내에서는 건축내외장재로서 가장 많이 이용되고 있으며 건축물의 Sash, Door, Panel 등 다양하게 적용된다.
|
BA |
냉간압연 후 광휘소둔 열처리 ( Bright Annealing) 하여 약간의 냉간 압연 (SKINPASS)을 한 제품으로 고도의 반사율을 가진 표면이다. 일반적으로 반사가 요구되는 가전제품이나 박판의 경우 많이 이용된다.
|
Chemical Coloring |
BA, Mirror, HL 제품표면에 환원성 강산수용액 중에서 전기화학적으로 표면을 산화시켜 생성된 산화막이 빛의 간섭을 일으켜 색상을 띠게 한 제품이다. 착색 후 경막처리하여 No. 2B 상태보다 내식성이 우수하며 표준색상은 갈, 청, 황, 적, 녹, 흑색의 6종류로 중간색상 및 중첩 등 다양한 색상이 가능하나 원자재의 표면상태에 따른 발색정도가 민감하여 균일한 동리색상으로의 재현성에 어려움이 있다.
|
Etching |
Mirror, HL, #8 등 제품표면을 선택적으로 부식시켜 의장효과를 낸 제품으로 화학 및 전기적 부식방법에 따라 시각효과가 달리 나타난다. 건축내외장재, Name Plate, 특히 엘리베이터 등에 주로 애용되고 있다.
|
표면 종류 |
특기 사항 |
Vibration |
Satin Vibration 연마라고 하며, 제조방법에 따라 상이한 Finish를 연출할 수 있고 Mirror 제품 표면에 무방향성으로 연속적인 동심원을 이루어 나타낸다. Etching & Coloring 등과 혼합하여 다양한 Pattern을 나타낼 수 있다. 주 용도로 고급 건축내외장재, 에스컬레이터 마감재, 엘리베이터 Door 등 다양하다.
|
Bead Blast |
선택된 제품위에 균일한 크기의 Bead 입자를 일정한 압력과 균일한 분포로 분사하여 표면의 광도를 조절한 제품으로 Sand 대신에 Bead를 사용한 것이다. 전체면적에 대해 Bead Blasting 할 수도 있고, Masking 방법에 의한 부분 Bead Blasting 할 수 있다. 주 용도로 무광택 Press Plate, 고급 건축내외장재 및 고급 엘리베이터 의장품에 사용된다.
|
Black Color |
BA, Mirror, HL 제품표면에 전기 화학적으로 표면을 산화시켜 빛의 간섭현상을 이용하여 표면에 색깔을 낸 제품이다. Coloring 후 경막처리하여 No.2B 상태보다 내식성이 우수하며 흑색으로 나타낼 수 있다. 원자재의 화학성분 및 표면조도에 따라 색감이 민감하여 계속 균일한 Color에 다소 문제점이 있다. 주 용도는 건축내외장재가 대부분이다.
|
Titanium |
진공상태에서 Stainless 표면에 Ti을 침투시켜 Ti와 친화력이 강한 N2, Ar, O2, C2H2 가 챔버 진공관 내에서 Arc Power 에 의해 분산되는 Ti-Arc Source 와 화학 반응을 일으켜 Stainless 표면에 Coating 되는 것으로 Gold 18k, 24k, Bronze, Blue, Black, Smoke-Gray, Silver, Rainbow 등과 같이 여러 가지 색상을 연출해 내는 것은 물론 Ti 은 Stainless 기본 성질보다 우수하여 바닷물에 대한 내식은 백금과 같을 정도로 우수하다. 이러한 사항들을 Ti-Coating 라하며 "SP-Ti30" 으로 칭한다.
|
Art HairLine |
Mirror 표면에 Computer Carving Machine을 이용하여 다양한무늬의 연마흔적을 나타내는 방법과, Masking 방법을 이용한 균일한 일정방향 연마흔적을 나타내는 방법등 다양한 기술적 개발이 가능한 제품이다. 이러한 Art HairLine 방법을 2-4회 연속 시행하여 제품표면이 입체감이 나타나게 할 수도 있으며, 시각적 효과를 나타내어 무늬 속에 무늬가 있는 것으로도 표현할 수 있다. 주 용도로는 고급 건축내외장재 및 고급 엘리베이터 의장품에 사용된다.
| |
쇼트 피닝
쇼트피닝은 직경 0.4-1.2mm의 수많은 강구를 원심력을 이용, 초속 수십 m/sec의 고속도로 스프링의
표면에 충격적으로 분사하는 작업이다. 이처리로 인하여 표면으로부터 0.2-0.3mm정도의 깊이까지
생성되는 가공경화와 압축잔류응력으로 스프링의 내피로성이 2배에서 10배까지 증가하는 효과를
가져온다. 또한 열간스프링에서는 쇼트피닝에 의하여 산화 스케일의 제거와 탈탄층의 변화 및 표면흠의
제거 효과가 추가됨으로 내피로성이 대단히 향상된다.
2. 쇼트피닝의 효과 :
- 표면의 툴마크 및 이쿨질을 제거한다.
- 산화스케일 및 탈탄층을 제거한다.
- 표면에 압축잔류응력을 생기게 한다.
- 표면층에 가공 경화를 발생시킨다. |
도 금
도금의 목적 : 표면의 녹방지 및 외관
도금의 공정 : 산 처리 =>> 수세 =>> 도금 =>> 수세 =>> 크로메이트(후처리) =>> 수세 =>> 탈수,건조
( 산 처리는 도금 전에 제품표면에 묻어있는 녹이나 기름등을 제거하는 과정이며,
크로메이트 는 도금한제품의 내식성을 높이기 위하여 크롬피막을 입히는 과정이며
대표적으로 천연색, 백색, 흑색, 국방색 등이 있습니다)
도금의 종류 : 도금의 종류는 크게 나누어 전기도금 , 화학도금 , 용융도금등이 있습니다.
- 전기도금 : 동도금 , 니켈도금 , 크롬도금 , 공업용(경질)크롬도금 , 아연도금 ,
주석도금 , 금,은도금등
-화학도금 : 전기가 통하지 않는 제품(플라스틱,목재,섬유,종이,도자기,석고 유리등)을
화학도금액에 넣어 도금
-용융도금 : 비철 금속을 녹여서 도금할 제품을 넣어 용융금속의 피막을 입히는 것
(ex: 전신주.가로등,가드래일,건축자재등)
아연 도금 |
|
대표적인 방식도금법 으로서 광범위한 분야에서 활용되고 있다. 철강의 방식에 극히 효과적인 것에 더해서, 도금욕 및 크로메이트 처리의 진보에 의해 외관 성능도 향상되어, 장식적용도로의 평가도 높아지고 있다. |
종 류 |
특 징 |
청화욕 |
옛부터 보급하고 있다, 가장 일반적인 도금욕. 2 차가공성이 양호하고, 균일전착성이 뛰어나고 있으므로, 특별히 작은프레스 제품과 복잡한 형상의 것에 적절한 도금법이나 고 농도의CN(청화소다)을 사용하므로 페수처리가 어렵다.. |
진케이트욕 |
청화욕 으로부터 CN을 없앤 알칼리욕으로 최근 급속하게 보급 되고있다.. 균일전착성이 뛰어나고, 프레스물과 볼트, 너트류에 적용되고 있다. |
산성욕 |
상기 두 가지 도금법에 비교해 전류 효율이 양호하고, 도금중에 수소 취성이 거의 생기지 않으며. 특히 고 탄소강, 열처리제품, 주물제품 도금에는 최적이며 CN을 사용하지 않으므로 폐수처리가 용이하다. |
각각의 도금법의 내식성은, 도금한뒤 후처리법에 의해 큰 차이가 생기기 때문에, 사용 목적과 환경에 맞은 적절한 도금 사양을 선택해야 할 것이다. 일반적으로 아연 도금은, 도금한 대로의 상태에서는 비교적변색, 부식하기 쉽기 때문에, 4종류의 크로메이트 처리를 한 것이 이용되고 있다. 각각의 크로메이트 처리의 개요는 아래 표와 같다. |
후처리의 종류 |
외관 색조 |
사용 조건· 목적 |
광택(백색) 크로메이트 |
청은백색 |
깨끗한 미관을 가지며, 내식성을 그다지 중시하지 않는 부품. |
유색 크로메이트 |
황금빛또는 무지개색 |
내식성을 중시한 부품. |
흑색 크로메이트 |
흑색 |
내식성이 좋으며, 장식 부품에도 많이 이용되며 차광목적 으로도 이용된다. |
녹색(국방색) 크로메이트 |
올리브색 |
가혹한 부식 환경에서 사용되는 부품. 위의 것들중 내식성이 가장좋다. |
아연 도금후, 특수한 염료 용액에 침지해 12색 에 착색하는 방법도 실용화되고 있지만 미관을 위해서지
내식성은 떨어집니다. 아연 도금의 특징을 열거하면, 다음과 같습니다.
- 기계가공된 비교적복잡한 형상의 소재에도, 거의 균일한 두께로 도금할 수 있고, 양산 가공도 용이
- 중성의 환경에서는 부동태 영역이 존재하여 내식성이 아주 좋으며, pH8∼ 12의 영역에 있어서의 부식은 특별히 적고 대기중의 부식 속도는 비 도금 제품의 약1/100정도입니다.
- 후처리 크로메이트 피막이 아연의 흼발생을 장기간 막기 때문 방녹 효과가 뛰어나게 된다.
- 다른 도금 가공비와 비교해, 극히 저가격으로 도금할 수 있다.
- 도금 후의 2차가공이 용이하다.
|
도금의 단위 : 도금의 두께단위는 미크론(micron)입니다. 즉 1mm를 1,000등분한 한 개의 눈금을
1μ(1미크론)이라고 합니다. 도금물체의 표면적은 평방데시미터 (dm2)라고 하며
1dm2 는 10cm×10cm = 100㎠ 입니다.
도금물체의 표면적 계산법은 다음과같습니다
{도금면적(dm2) = 소재무게(kg) ÷ 소재두께(mm) ÷ 소재비중×2×100}
도금의 장점과 단점
도금종류 |
개요 및 용도 |
장점과 단점 |
전기 도금 |
전해 용액중에서 물건을 음극으로서 통전하여 표면에 도금 금속을 석내케 하는 것, 장식, 방녹, 기능과 다양한 목적으로 도금하며, 비교적 염가이고, 적절한 금속 피막을 부여할 수 있기 때문에, 자동차와 음향, 항공기, 통신기, 컴퓨터부품, 장신구, 건축자재등에 사용
|
(장점) 다종 소량품까지 가공 가능하며. 다채로운 금속
질감을 부여할 수 있고, 고가의 금속에 뛰어난 특성과
양호한 밀착성을 가진 피막을 얻을 수 있다. |
(단점) 형상에 따라 도금후 얼룩이 생길 수 있고.독성이
강한 CN을 사용하므로 폐수처리가 어렵다. | |
무전해도금 |
용액중의 환원 반응을 이용, 제품 표면에 도금 금속을 석내케 하는 것, 금속부터 비금속까지 넓게 도금이가능하고, 도금후 정밀도도 극히 높기 때문에, 주요하게 기능을 중시하는 공업적용도에 널리쓰이고 있으며. 플라스틱 도금의 기초용으로서 꼭 필요한 도금법.
|
(장점) 전착성이 균일하고. 부도체 소재에도 양호한
밀착성을 가진 도금을 할 수 있다. 금속, 비금속에 도금이 가능하다. |
(단점) 소재에 따라 복잡한 사전처리가 필요하며. 폐수
처리가 어렵다. | |
진공 도금 |
용기 내를 진공으로 하여, 금속과 산화물, 등을 가스화 혹은 이온화해 물건 표면에 증착 시키는 것으로. 진공 증착과 스팩터링, ion 플레이팅, ion질화, ion 주입등 으러가지 방법이 있고, 장식, 기능의 분야에서 활용.특히 반도체 제조에 불가결의 기술이다.
|
(장점) 대부분의 금속 소재, 비금속 소재도 처리 가능하고., 장식성이 뛰어난 초 경질피막을 얻을 수 있다. |
(단점) 일반적인 전기 도금과 비교, 고온 처리 해야되고, 비용도 높다. | |
용융 도금 |
아연과 주석, 알루미늄등의 금속을 용해한 액 중에 물건을 넣고, 각각의 금속을 부착시키는 것으로, 대표적인 예가 아연과 알루미늄을 도금한 강판으로 비교적대형 구조물과건축자재, 가드레일, 가로등, 전신주 부품등에 많이 이용.
|
(장점) 면적의 큰 것, 중량물등의 방식 도금에 적절하고 도금 하기에 따라 수10년의 방식성을 가질 수도 있다. |
(단점)꽤높은 고온욕작업이고.도금의 종류가 제한된다. | |
전착도장 |
전기 도금과 지극히 닮은 이미지의 기술로, 수계 도료의 (안)중에 피처리물을 침지, 이것을 음극또는 양극으로 하고, 직류 전기를 통해 도막을 형성시키는 것으로. 전자를 양이온 전착도장, 후자를 음이온 전착도장이라고 말한다. 방녹 목적으로는 흑색이 많이 이용.
|
(장점) 피처리물의 형상에 좌우되지 않고 균일한 도장을 할 수 있다. 일정한 관리를할 수 있다. 도료 손실이 적고, 여과에 의해 도료 회수를 할 수 있다. 화재의 걱정이 없고 위생적. |
(단점) 후막화를 할 수 없다. 전기 용량이 크다. 색대체가 곤란. | |
양극 산화 |
황산과 수산등의 전해 용액중에서 물건을 양극으로 하고, 통전해 표면에 산화 피막을 생성시키는 것으로, 각종 새시와 문, 필기도구, 카메라압판, 명찰로부터, 항공기와 정밀 기계, 계측 기기등넓게 이용.
|
(장점) AI의 양극 산화 피막의 두께는 장식과 방식을 목적으로 한 것에서는4∼ 10μ 의 범위로(에서) 이용되고, 착색가능하며 용도는 넓다. |
(단점) 2차가공이 곤란하다. 다른 금속 재료는AI 같은 두꺼운 산화 피막은 생성되지 않다. | |
도장 |
도장 방법에 따라, 정전 도장, 전착도장, 분체 도장등이 있어, 어느 제품에나 광범위하게 활용되고 있다. 다채로운 색채화가 가장 용이한 기술.
|
(장점) 금속으로 하는 공업 재료의 최종 마무리 가공으로서도 많이 이용되고 있으며. 처리 방법이 간편하다. |
(단점) 일반적으로 표면 경도가 낮은 것과, 용제 휘발형의 도료로 공해의 문제를 안고 있다. | |
표면 경화 |
철강 재료에 대한 침탄과 질화처리, 고주파 담금질이 대표적이며. 최근에는 황화 처리를 시작하고, Al, Cr, Ti, W등의 금속과 그 탄화물을 소재 표면에서 확산 침투시키는 수법이 개발되고 있다. 처리법도 가스, 염욕, 진공, ion등.
|
(장점) 특별히 단순 형상의 플라스틱 성형 품등에서는 메탈릭화가 용이하게 행할 수 있다. 화상을 인쇄한 박에 의해,임의의 색의 stamping가능. |
(단점) 소재와의 밀착성에 난이하고. 피막이 지극히 얇고, 약하기 때문에, 이것을 보호하는 피막이 필요하다. | | |
장식도금의 종류와 용도
상품 가치를 좌우하는 요소의 하나로, 장식 외관, 즉 미관이 있다. 특별히 장식적 용도의 상품에 있어서는,
미관이 생명이라고 말해도 과언이 아니다. 금속, 플라스틱 등, 직접 눈에 보이거나, 조작되거나 하는 상품들은
사용목적에 따라 도금을 하므로 그 상품의 가치를 높여 줄 것입니다. 이 장식 목적을 위해서 광범위한 분야에서
활용되고 있는 표면 처리 기술이, 전기 도금입니다. 금속과 플라스틱등의 소재에, 뛰어난 밀착성을 가지는 각종의
도금을 하므로 인하여 색조, ,질감 등을 가진 새로운 금속 표면을 가지므로, 고급화, 정밀함, ,조작성, 금속감, 청결,
내식성등의 다양한 기능이 부가됩니다.
|
대표적인 용도 |
장식상의 특성 |
외관의 종류 |
도금의 종류 |
기초 |
중간 |
마무리 |
자동차 외장품 (범퍼, 드아핸들, 그릴, 와이퍼, 휠 너트, 휠캡)
|
고급화, 방녹, 금속감 (수지 소재) , 오염 방지, 내식성, |
광택, 반광택 , 색조 (크롬, 흑색) |
동 |
이중니켈 |
크롬, 흑색 크롬 |
반광택 니켈 |
광택 니켈 |
크롬, 흑색 크롬 |
동 |
반광택 니켈-사치라이트 니켈 |
크롬, 흑색 크롬 |
음향, 가전, 편기등 (손잡이, 스윗치등)
|
고급화, 정밀함, 조작성, 방현성, 오염 방지, 금속감 (수지 소재) , 위생적 |
무광택배지조 |
동, 니켈 |
베로아니켈, 실키-니켈, 파르브라이트 니켈 |
크롬, 금, 주석-코발트, 동-니켈 |
반광택배지조 (사치라이트) |
동, 니켈 |
사치라이트 니켈 |
크롬, 금, 주석-코발트, 동-니켈 |
모양 (소재 가공) (헤어라인, 스핀, 리지, 흑색등) |
동 |
니켈 |
크롬, 금, 주석-코발트, 동-니켈 |
색조 (크롬, 크롬색, 금빛, 은백색, 흑색등) |
동 |
니켈 |
크롬, 금, 주석-코발트, 동-니켈 |
세면 쇠장식, 샤워,
손잡이등 냉장고문 핸들 (ABS수지 소재)
|
고급화, 방녹, 오염 방지, 위생적 |
광택, 색조 (크롬) |
동 |
반광택 니켈-광택 니켈 |
크롬 |
카메라 외장품 (ABS수지 소재)
|
고급화, 방현성, 정밀함, 금속감, 내식성 |
무광택배지, 색조 (크롬, 흑색) |
동, 니켈 |
베로아니켈, 사치라이트 니켈 |
크롬, 흑색 크롬 |
의자, 책상등의 가구 철물 (파이프류)
|
고급화, 방녹, 오염 방지 |
광택, 무광택배지,
색조 (크롬) |
동, 니켈 |
반광택 니켈-광택 니켈, 베로아니켈 |
크롬, 흑색 크롬 |
전시용 쇠 장식
|
고급화, 광반사성, 위생적, 오염 방지 |
광택, 색조 (크롬, 금빛) |
|
광택 니켈 |
크롬, 금 |
시계 , 라이터, 안경테
|
고급화, 정밀함, 오염 방지, 내마모성 |
모양 (소재 가공) (헤어라인, 다이어컷, 리지등) , 광택, 반광택, 색조 (크롬, 금빛, 은빛, 흑색) |
동 |
광택 니켈 |
크롬, 금, 로지움,,금빛 |
가방 부속, 버클등 장신구
|
고급화 |
광택, 모양 (헤어라인등) 색조 (크롬, 금빛, 고미) |
동 |
광택 니켈 |
크롬, 금, 로지움 , 금빛 |
조명 기구등의 인테리어 철물
|
고급화, 정밀함, 다양화 |
광택, 색조 (크롬, 금빛, 고미, 화이트 브론즈, 박래색등) |
동 |
광택 니켈 |
크롬, 금, 금빛, 니켈, 동, 은, 놋쇠, 화성 처리등 |
양식기, 하우스 웨어
|
고급화, 위생적, 오염 방지, 방녹 |
광택, 모양 (펄 가공등) , 색조 (크롬, 은빛, 금빛) |
니켈 |
광택 니켈 |
크롬, 은, 금, 주석-니켈 |
각종 합금도금
소비 층의 다양화로 인해, 장식 도금으로 백색계, 흑색계, 금빛계와 다채로운 금속 색조를 가진 합금 도금이 실용화되어, 음향 부품과 가전 부품을 중심으로 넓게 이용되고 있습니다.. 합금 도금은, 도금 피막의 합금화 율에 의해 색조가 미묘하게 변화하는 성질을 가져 극히 고도의 욕 관리 기술을 필요로 하는 도금이라고 말할 수 있습니다. 그런 만큼, 종래에 없는 특이한 색조를 제공할 수 있을 가능성이 있으며, 이용자측에 있어서도 매력이 있는 도금 법이라고 말할 수 있는 것입니다.
합금 도금은 기본이 되는 금속에 의해서, 다음 표 같게 분류됩니다.
|
|
도금 피막의 내용 |
외관과 특장 |
주요한 용도 |
주 석 계 |
주석-코발트
|
크롬색. 코발트가 증가하면 검은 빛을 띤다. 바렐 도금으로의 양산 가능. |
손잡이, 스윗치등의 음향
부품, 사무 용품, 장식품등. |
주석-니켈
|
검은 빛을 띤 우아한 색조. 변색이 잘 안되며, 내식성이 양호. |
사무 용품, 가정용품, 등. |
주석-동-아연
|
소위 대용 금도금과 맞 먹는다. 적색 부터 백색까지의 금빛.
|
장신구, 조명 기구, 잡화등. |
주석-니켈-동
|
약간 붉은 빛을 띤 흑색으로, 중후한 색조. 내식성, 내 마모성이 양호. |
장식품, 사무 용품, 자전차 부품, 등. |
동 계 |
동-석
|
브론즈 도금과 비슷하다. 주석이 증가하면, 붉은 빛→ 노랑→ 흰색으로 변화한다. 내식성이 양호해 평활성이 우수하다. |
장식품, 사무 용품,등 |
동-아연
|
놋쇠 도금과 비슷하다. 합금 비율에 의해 금빛은 붉은 빛으로부터 백색 변화한다. |
장신구, 잡화, 쇠장식, 조명 기구등. |
동-니켈
|
분홍계 금빛으로부터 희미한 금빛. 내식성이 양호. |
장식품, 잡화등. |
니 켈 계 |
니켈-코발트-
텅스텐
|
전연성이 뛰어나고, 내식성도 양호. |
장식품, 사무 용품,등. |
니켈-철
|
기초, 중간 도금으로서의 니켈 도금의 대체로서 이용된다. 평활성이 좋고, 후가공성이 양호. |
장식 크롬 도금등의 기초. 중간 도금. |
각종 흑색도금
흑색 크롬 도금
흑색 피막이 얻어지는 대표적인 도금이다. 고급 카메라의 위 덮개, 혹은 자동차와 오토바이의 각 부품에 넓게
이용되고 있는 것 외에 통신기부품 (방열 효과를 목적으로 한 쉴드 케이스등) , 시계측, 사무기 등에 활용되고
있습니다.도금 직후의 피막에 광택이 없는 경우는, 후처리로서, 왁스 마무리, 규소 마무리등을 할 필요가 있고,
도금 욕 조성과 전착조건에 의해 다르기 때문에, 각 공장에서 미묘하게 다른 경우가 적지 않습니다. 내 마모성이 부족하기 때문에, 마찰을 동반하는 부품에는 부적합이지만, 후처리에 독자의 노하우를 가지고 있는 공장에서는 비교적 내 마모성이 뛰어난 흑색 크롬 도금을 제공하고 있는 곳도 있습니다.
|
아연 도금 (흑색 크로메이트)
광택 아연 도금 뒤에, 은염을 함유한 욕중에 침지해 얻어지는 흑색 크로메이트 피막은, 내식성이 양호하기 때문에, 외관 향상, 즉 부가 가치 향상의 목적과 공히, 자동차와 볼트, 너트, 각종 쇠장식류, (내장품) 등에 이용되고 있다. 고급 양산 살대에도 이용되고 있습니다. 면적이 넓은 것은 균일한 흑색이 어렵고 건조 후 얼룩등이 생기지 않도록, 주의해야 할 것입니다. |
흑색 니켈 도금
도금 직후의 피막은 광택이 없기 때문에, 일반적으로 광학 기기의 내장 품등에 이용되고 있다. 내식성은 흑색 크롬 도금으로 비교하면, 많이 부족한 편입니다. 그리고 동과 놋쇠 도금 상에 흑색 니켈 도금을 하고, 부분적으로 버프 연마를 하여 동의 색조와 놋쇠의 색조에 흑색이 띠며.이런것은, 가구 철물과 조명 기구, 장신구, 등에 많이쓰입니다 |
흑색로지움도금
비교적 새로운 도금법 으로, 내식성이 뛰어나고, 중후한 색조와 함께, 안경테와 시계부품등에 이용되고 있습니다. |
. 방식도금의 종류·와 용도 |
도금의 종류 |
특징과 용도 |
청화욕
|
가장 일반적인 아연 도금으로, 옛부터 활용되고 있다. 프레스물, 볼트, 너트등에 사용되고, 2차가공성이 양호하다. |
진케이트욕
|
청화욕의 독성이 강한CN-를 없앤 알칼리욕으로, 프레스물, 볼트, 너트류에 도금을 주로하며. 균일성이 양호하다. |
산화욕
|
알칼리욕에 비교 전류 효율이 좋기 때문에, 고 탄소강 및 주물등에도 도금이 잘 돼며, 도금 중에 수소취성이 거의 생기지 않으며. 또 처리 방법에 의해서는 스테인레스상에도 도금이 가능하다. |
카드뮴 도금
|
특별히 염분에 대한 내식성에서는 아연 도금보다도 뛰어나고 있기 때문에, 항공기 부품과 선박 부품등의 중요 부품에 이용되고 있다. 사용 목적에 따라, 유색 크로메이트와 광택 크로메이트도 가능하다 |
주석-아연 합금 도금 (70%Sn-30%Zn)
|
염분에 대한 내식성에서는, 카드뮴 도금과 닮은 성질을 가지고 있다. 카드뮴 도금에 비해서, 도장 밀착성, 연전성등의 후가공성이 뛰어나고 있기 때문에, 그 특성을 이용한 분야에서 이용되고 있다. 저접촉 저항의 특성도 가지고 있어, 전기 부품에 많이 이용되고 있다. |
아연-니켈 합금 도금 (Zn-5∼ 10%Ni)
|
고내식성을 자랑하는 방녹도금으로, 유색 크로메이트를 한 것은, 아연 크로메이트의 수배이상의 내식성을 가지고 있다. 수소 취약성이 없기 때문에, 방녹을 중시한 기능성 부품을 중심으로 보급해 가는 것이라고 생각된다. |
아연-철합금 도금 (Zn-0.2∼ 0.7%Fe)
|
고내식성을 자랑하는 방녹도금으로, 평균 5μ 의 도금으로 유색 크로메이트를 한 것은, 염수 분무 시험으로 적청 발생까지2,000시간 이상이라 매우 높은 내식성을 나타낸다. 일반적으로 진케이트욕 타입이 이용되며 , 도금 피막의 특성은, 종래의 진케이트형아연 도금과 동등하며. 광택, 유색, 흑색의 각크로메이트가 가능하다. |
방녹도금의 특성 비교
|
도금의 종류 |
아연 |
주석-아연 합금 |
아연-니켈 합금 |
청화욕 |
진케이트욕 |
산성욕 |
특
성 |
경도 (Hv)
|
60∼ 80 |
90∼ 120 |
70∼ 90 |
14.5∼ 14.9 |
150∼ 170 |
균일전착성
|
A |
A |
B |
A |
B |
수 소 취 성
|
C |
C |
A |
B |
A |
주물에로의 도금
|
C |
C |
A |
A |
B |
프레스물의 도금
|
A |
A |
A |
A |
A |
나사, 볼트의 도금 |
A |
A |
A |
A |
A |
동,니켈,크롬 및 플라스틱 도금
장식 크롬 도금과 총칭되는 도금으로, 금속 소재, 플라스틱 소재를 묻지 않고 장식 도금의 주류를 이루는 것들입니다. 초기 가공과 기초 도금의 종류에 의해서, 단순한 광택 외관만 되지 않고, 리지, 헤어라인, 스핀, 다이어컷, 새틴 (반광택배지) , 베로아, 펄등, 다채로운 외관이 용이하게 부여되기 때문에, 크롬 도금이 가지는 중후한 금속 질감, 청결감, 정밀함과 함께, 모든 분야에서 넓게 이용되고 있습니다. 장식 크롬 도금은 일반적으로, 동-니켈-크롬 도금이라고 표현되는 것이 많고, 기초 도금으로서, 동 혹은 니켈 (반 광택, 광택등) 이 행해지고 있는 것이 보통이며. 소재에 의해서는 동 도금이 생략되는 경우도 있습니다. 크롬 도금으로는 장식성과 공히 내식성도 중요한 요소이지만, 보다 내식성이 요구되는 자동차 부품등에서는, 이중니켈 도금으로 하거나, 트리니켈 도금을 하고, 마무리를 크롬 도금하므로, 고 내식성이 보장되고 있습니다 |
마무리 도금 |
색조, 경도, 내마모성등 부여 |
기초 도금(2) (외관, 내식성 부여) |
광택, 반광택, 새틴, 베로아, 실키-, 펄 (중간 연마) |
기초 도금(1) (내식성 부여) |
광택, 리지부여 |
초기가공 |
마무리 연마 (광택) , 리지 (호닝, 샌드 블레스트) , 헤어라인, 스핀, 다이어컷, 각종 모양 |
장식 크롬 도금의 다채로운 외관은, 이러한 피막 구성에 의해 부여되며, 장식 크롬 도금은, 도금의 종류, 두께에 의한 등급 분류 및 내식성의 기준이 규정되고 있으며. 마무리를 크롬 도금으로 하지 않고, 니켈 도금으로서 약간 붉은 빛을 띤 백색 광택으로 하거나, 광택 동 도금으로 마무리하는 것도 적지 않습니다. |
일반적인 도금 종류와 다른 분류는 아니지만, 플라스틱 소재에 전기도금을 하는 것으로 장식 도금 중에서
큰 비중을 차지하고 있는 도금으로, 플라스틱 소재와 부품의 다양화로 많이 각광 받는 도금 기술 중의 한
가지이며, 플라스틱 도금은 밀착성이 무엇보다도 중요하고, 그 시험 방법은 여러 가지 있지만, 일반적으로는,
소재가 ABS이고, 적절한 사전 처리가 행해진 것이면, 그 도금 밀착력은500∼ 1,600g/cm(UL합격 기준은180g/cm) 는 달성되고 있다고 생각해도 좋습니다. |
다크로처리
다크로(DACRO)란?
다크로처리는 다크로액을 침적 및 탈루(Dip & Spin)도장방식으로
도포후, 건조로를 통과하면 고내식성의 피막을 형성합니다.
다크로 처리액은 다크로 딥(Dacro Dip)이라 부릅니다. 기본적인 조성은 플레이크상(Flake)의 특수금속아연, 무기화합물 등입니다. 다크로 딥에 피처리물을 침지한 후 건조로에서 약 320℃로 가열 하면 아연플레이크를 상호 결합하는 다크로 피막이 형성됩니다.
다크로 처리의 방청시스템은 아래와 같습니다. 1)아연입자의 자기희생보호작용 2)무기화합물에의한 금속소재의 부동태화작용 3)아연플레이크와 무기화합물의 장벽작용
|
|
 |
Dip & Spin 도장 다크로 피막구조 |
특 징
우수한 내식성을 갖고 있습니다: 약 6~10μm도막으로 염수분무
시험에서 최고1000시간까지 적청발생이 없습니다.
수소취성의 염려가 없습니다. : 처리공정 중 산처리, 전해공정이 없기 때문에 전기아연도금처럼 고장력 볼트, 스프링류 등에 수소 취성이 발생되지 않습니다.
복잡한 형상도 처리가능 : 파이프 내부도 처리 가능합니다.
알미늄과의 접촉부식(전식)방지에 효과가 있습니다.
다크로 처리위에 다른 도장도 가능합니다.
어떤금속도 처리 가능합니다. : 철, 주물, 소결금속, 알미늄 다이 케스트, 스텐레스 등
공해염려가 없습니다 : 전기아연도금과 달리 수세공정이 없으므로 폐수공해 발생이 없습니다.
종래 아연도금에- 비해 높은 내열성과 우수한 방청 능력
도료와의 밀착성이 우수하며, 얇은 막을 형성하는 도장처리물의 하지처리
로서, 방청시스템 형성
|
|
 |
강교용 고장력 볼트 |
공 정
탈지(기름제거)-탈청(스케일, 녹 제거)-도장- 건조가 기본공정 입니다.
도장공정에는 3가지 방식이 있습니다. 1)Dip & Spin 방식 : 가장 일반적인 방법으로 대부분의 처리에 권장됩니다. 2)Dip & Drain방식 : 대형처리물에 적당합니다. 3)Spray방식 : 외관을 특히 중시하는 부품에 적당 하나 피처리물 특성에 따라 방청능력이 저하될 수 있습니다.
도장후 2단계(예열100℃, 본열320℃)의 건조 과정을 거쳐 피막을 완성시킵니다
|
|
|
 |
Dip & Spin공정 |
각종 도금의 특성비교(염수분무 결과표)
|
내식성능 |
수소취성 |
충격에 의한 내식성 |
외관상태 |
비고 |
다크로처리
|
600시간 이상 |
무발생 |
양호 |
은회색(무광) |
|
전기아연도금
(크로메이트)
|
90시간 이상 |
발생 |
보통 |
은백색/유광,유색 |
|
카드뮴
(크로메이트)
|
120시간 이상 |
발생 |
보통이하 |
은회색/유광,유색 |
|
용융아연도금
(크로메이트)
|
300시간 이상 |
발생 |
양호 |
은백색/반광 |
|
비고) 1. 내식 성능 : 염수분무 시험에 의한 비교
2. 수소취성 : 도금한 금속의 경도가 HRS 40 혹은 HRC32이상인 | |